Using advanced closed-cell technology, emew's copper liberators offer a fast, safe and efficient alternative to conventional copper refinery bleed technology. This innovative cell design improves copper and impurity control over a range of concentrations, resulting in a high-grade, saleable copper cathode from the refinery bleed. With improved energy and operational efficiencies, our technology delivers simpler processes and better financial returns, while reducing environmental impact.
How emew compares to conventional metal recovery from copper refinery bleed
emew clean technology
- Better operational efficiency with no cell sludge, no anodes, better impurities control and arsenic level control
- Pure copper produced for sale on first pass, increasing smelter capacity
- Additional revenue stream from nickel from bleed recovered as high-purity carbonate
- Improved health and safety with no acid mist or arsine gas generation
- 30-70% energy savings and reduced reagent use
Conventional liberators
- Operational and safety issues from hazardous sludge formation and uncontrolled impurities
- Inconsistent output and higher operating costs with sludge recycle
- Loss of nickel value from bleed recovered as crude nickel sulfate
- Serious health and safety concerns from acid mist and potential arsine generation
- Energy intensive electrolysis in the liberators and crystallization/ evaporation processes with higher acid consumption
Replacement of copper liberators for White Pine copper refinery
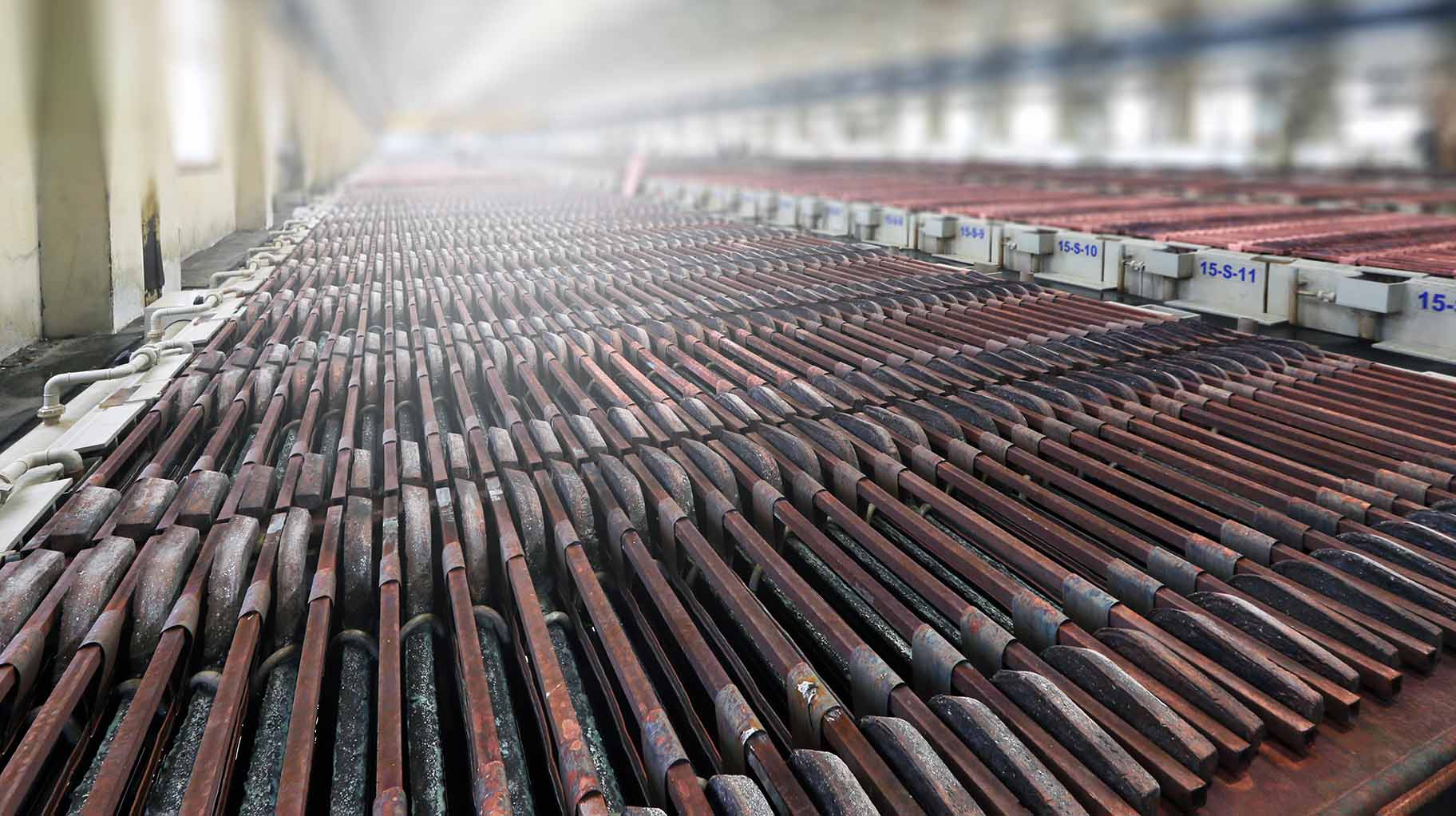
Challenge:
Before implementing emew technology, the White Pine copper refinery used spent anodes to deposit liberator copper with impurities. These required shipping for reprocessing, leading to increased costs, maintenance and safety risks, including handling arsenic-laden materials and managing acid mist and toxic gasses.
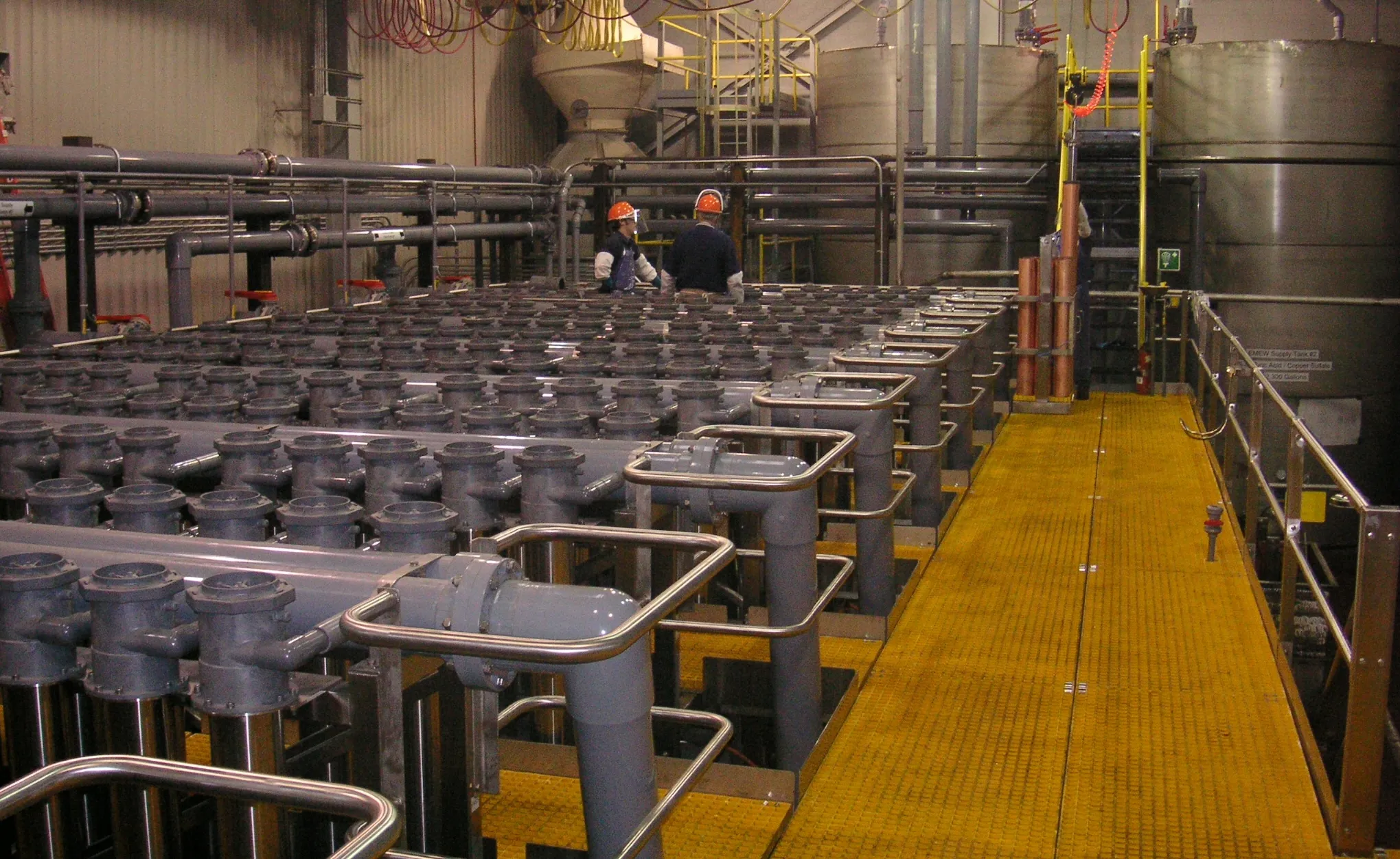
Solution:
In 2007, the White Pine refinery installed a 720-cell emew system to replace their copper liberators. The emew plant operates in a fully closed mode, eliminating toxic gases and acid mist, without the requirement for heavy electrode handling. This on-site solution also eliminated the need for 2,750 metric tonnes of liberator cathode to undertake a 3,200 km round trip, driving significant efficiency, environmental and financial working capital improvements.
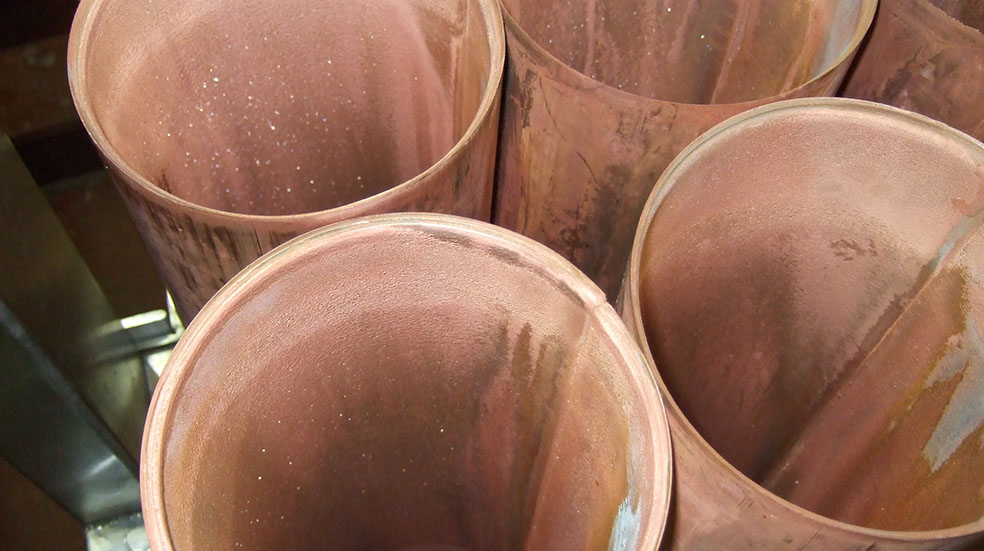
Result:
The customer produced pure B115 grade copper on first use of the fully installed emew system, with additional cost-effective and environmentally friendly benefits:
- 85% reduction in transport for impure cathode
- 35% reduction in power consumption per kg of copper removed
- 4% increase in production, adding $30 million per year in copper value that was trapped in working capital transporting spent anodes back to the smelter