How emew compares to conventional precious metal refining
emew clean technology
- Negligible to minimum sludge generation and lower carbon emissions
- Improved safety and operational efficiency due to closed and automated system
- Consistent, high purity silver from low-grade feeds, plus direct sale of copper cathodes from by-product copper
- No anodes casting and remelting; leaching done instead of anode casting
- Low working capital and inventory required, increased efficiency and smaller footprint
Electrorefining (Moebius)
- Typically 90% more sludge generation, requiring transport to processing
- Operator risk exposure to anode handling and acidic electrolyte
- Difficult to produce high-purity silver from low-grade feed; copper value lost
- Anodes casting and spent anodes remelting required with additional cost and labor
- Significantly higher working capital, more inventory, harder to scale and additional space required
In addition, lack of acid regeneration and transport/disposal costs increases the environmental impact of this method. Our closed-loop clean technology solution consistently produces saleable high-purity silver alongside copper cathodes, with less water consumption, minimal sludge generation and a 40% smaller footprint than conventional silver chloride recovery processes.
emew clean technology
- Automated one-step process to consistently recover high-purity silver (typically .9999+)
- Saleable high-grade silver production and copper products recoups 20-80% of system cost
- Pure silver on first pass enabling increased refinery capacity
- Lower carbon emissions and water consumption, minimal wastewater and acid reused
- 40% smaller footprint than silver chloride processing and easier to scale modularly
AgCI
- Complex, slow, multi-step process requiring manual input, with inconsistent results
- Significantly higher working capital, with lower purity output and lost copper value
- Higher operating costs for silver production due to recycling to smelter and refinery
- 90% more sludge generation, increased water consumption and wastewater, no acid regenerated
- More space required than emew system, difficult to scale
How emew’s silver refining process solved a Moebius operational challenge
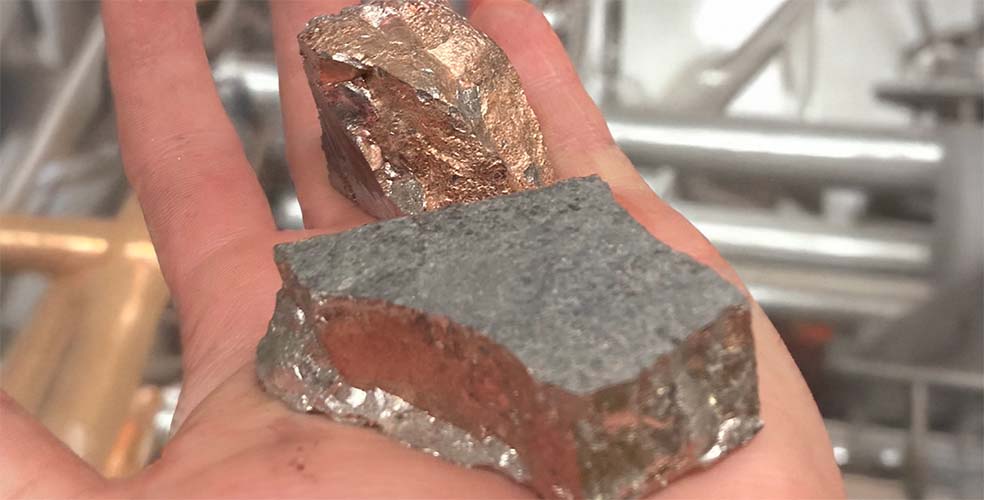
Challenge:
Traditional Moebius silver refining requires substantial silver inventory, significant manpower, frequent replenishment of silver nitrate electrolyte due to copper contamination and disposal of copper hydroxide sludge. For our customer, this labor-intensive process was leading to increased downtime and costs, exposing several operational inefficiencies, environmental issues and significant financial burdens.
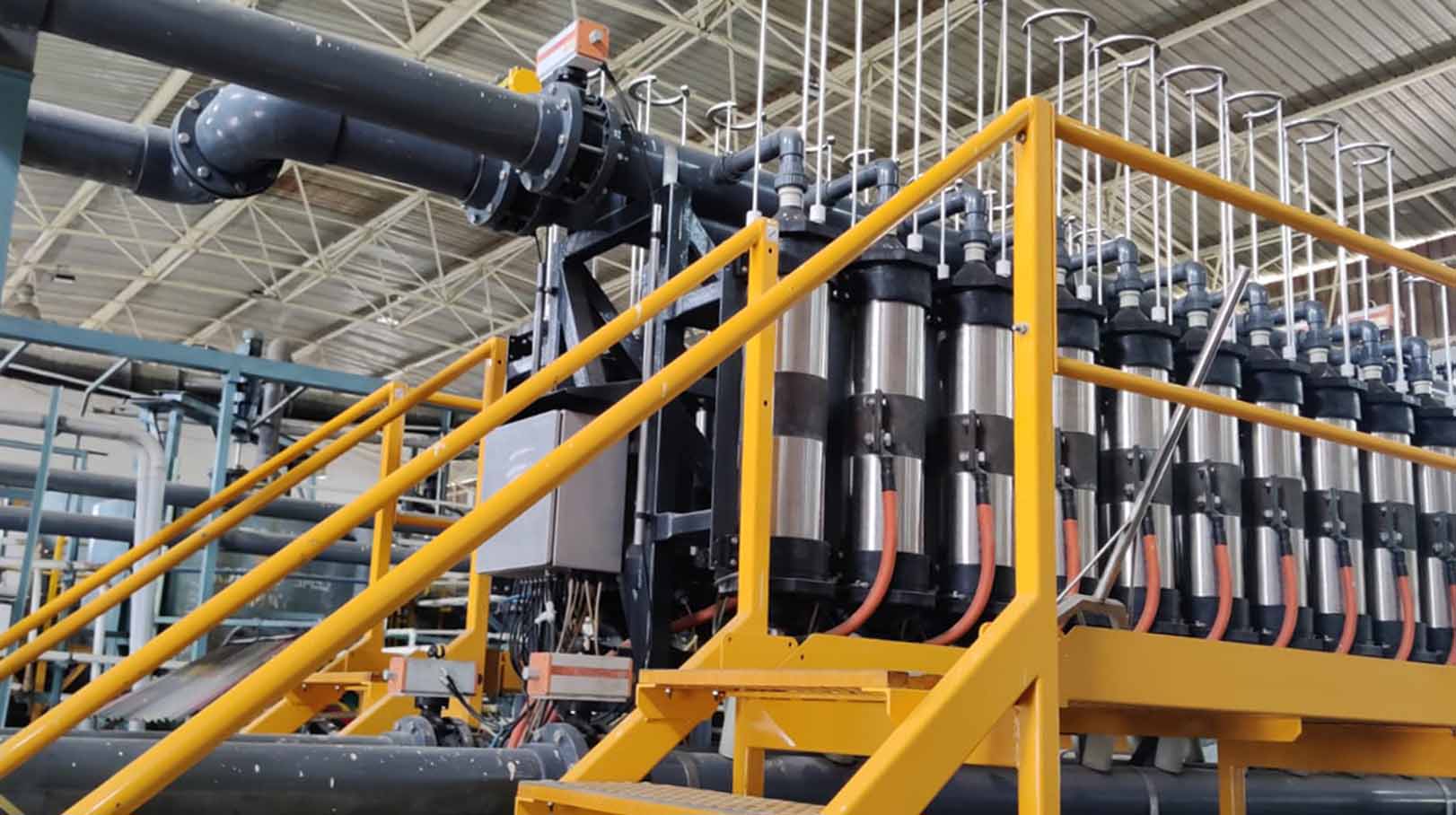
Solution:
Our customer transitioned to emew’s silver processing technology, which uses high-flow electrowinning cells to produce high-purity silver and efficiently manage and recover copper. This reduced contamination and eliminated the need for frequent electrolyte replenishment, resulting in a more sustainable, cost-effective and efficient operation.
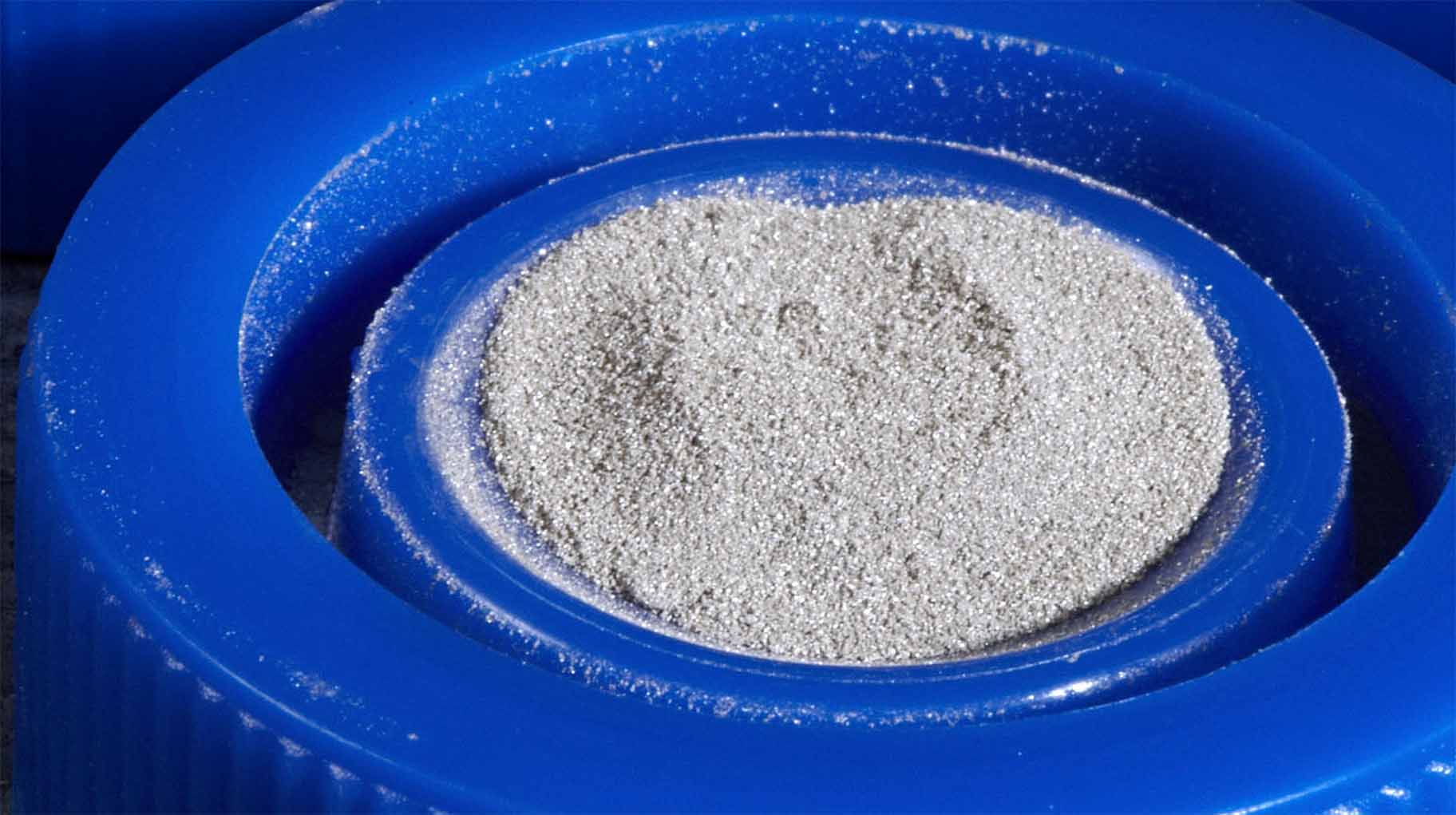
Result:
This innovative emew closed-loop process for silver recovery allowed for continuous operation with minimal downtime and less manual intervention, providing a number of benefits:
- Consistent recovery of higher purity silver at ~99.99%
- 20% reduction in operating costs and 25% reduction in capital expenditure
- 40% less floor space required
- 30% reduction in labor costs
- 85% reduction in silver inventory
- Additional revenue from recovered copper
- Lower environmental impact due to reduced waste production
- Continuous operation with minimal downtime and less manual intervention