emew’s suite of technology solutions provides an innovative approach to industrial wastewater treatment, focusing on efficient metal recovery and sustainable practices. Our technology offers a closed-loop system that not only treats wastewater but also regenerates acid, significantly reducing waste and environmental impact. By incorporating our solutions, businesses can effectively manage copper and other metal contaminants in their wastewater, minimize acid loss, and reduce operational costs. The result is a streamlined process that supports both environmental sustainability and improved financial performance.
Pure copper recovery from etching and pickling baths
How emew enhances the etching and pickling process
emew clean technology
- Eliminated downtime and consistent pickling times
- High revenue and ROI with consistent high-grade copper recovery for resale
- Closed loop process with no waste reduces acid purchase and acid waste handling
- Reduced Scope 3 emissions, with no dumping or haulage
- Simple, efficient process allows reallocation of labor from tank dumping
Conventional treatment
- 4% less uptime with increased risk for poor product quality
- Loss of additional revenue, additional waste disposal fees and labor costs
- 100% acid loss during cleaning and dumping requires acid handling, purchase and storage
- Scope 3 emissions by third party processing or sludge disposal
- Additional labor costs for tank dumping
$1m savings from emew copper replacement of copper sulfate plant
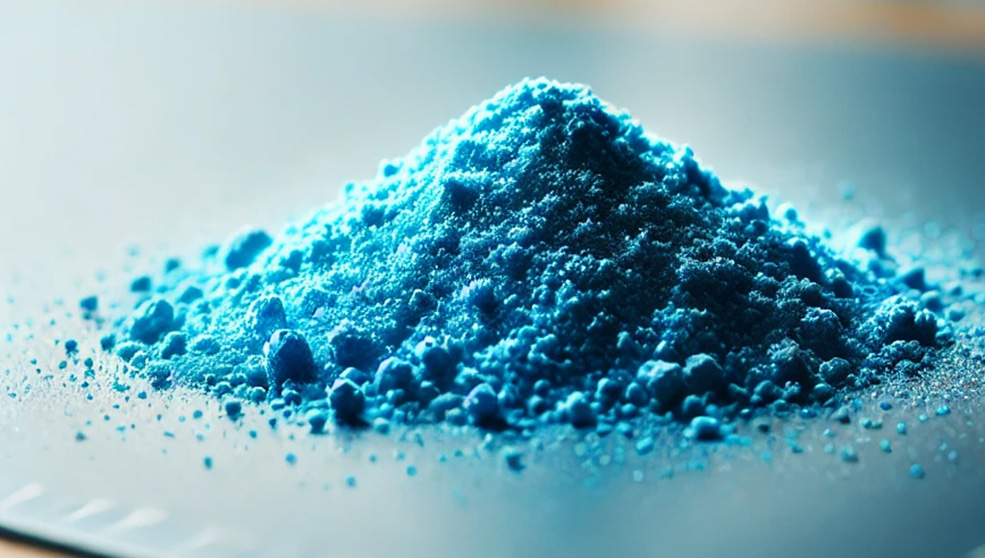
Challenge:
The Phelps Dodge (now Freeport) El Paso Rod Mill – one of the world’s largest manufacturers of continuous cast copper rod – faced challenges with its copper rod surface-treatment process. The method used a sulfuric acid and hydrogen peroxide solution that needed periodic replacement, producing large volumes of spent solution to be sent to a copper sulfate crystallization plant. This process was labor and energy-intensive, costly and inefficient.

Solution:
Phelps Dodge (now Freeport-McMoRan) engaged emew to replace the copper sulfate plant with an advanced vortex electrowinning system, recovering 1700kg/day of copper and regenerating sulfuric acid to return to the etching and pickling process. The emew system produced the highest purity cathode for direct use in the rod mill, regenerated acid for rod cleaning operations and simplified operations through improved safety, zero discharge, and significant water, energy and labor reduction.
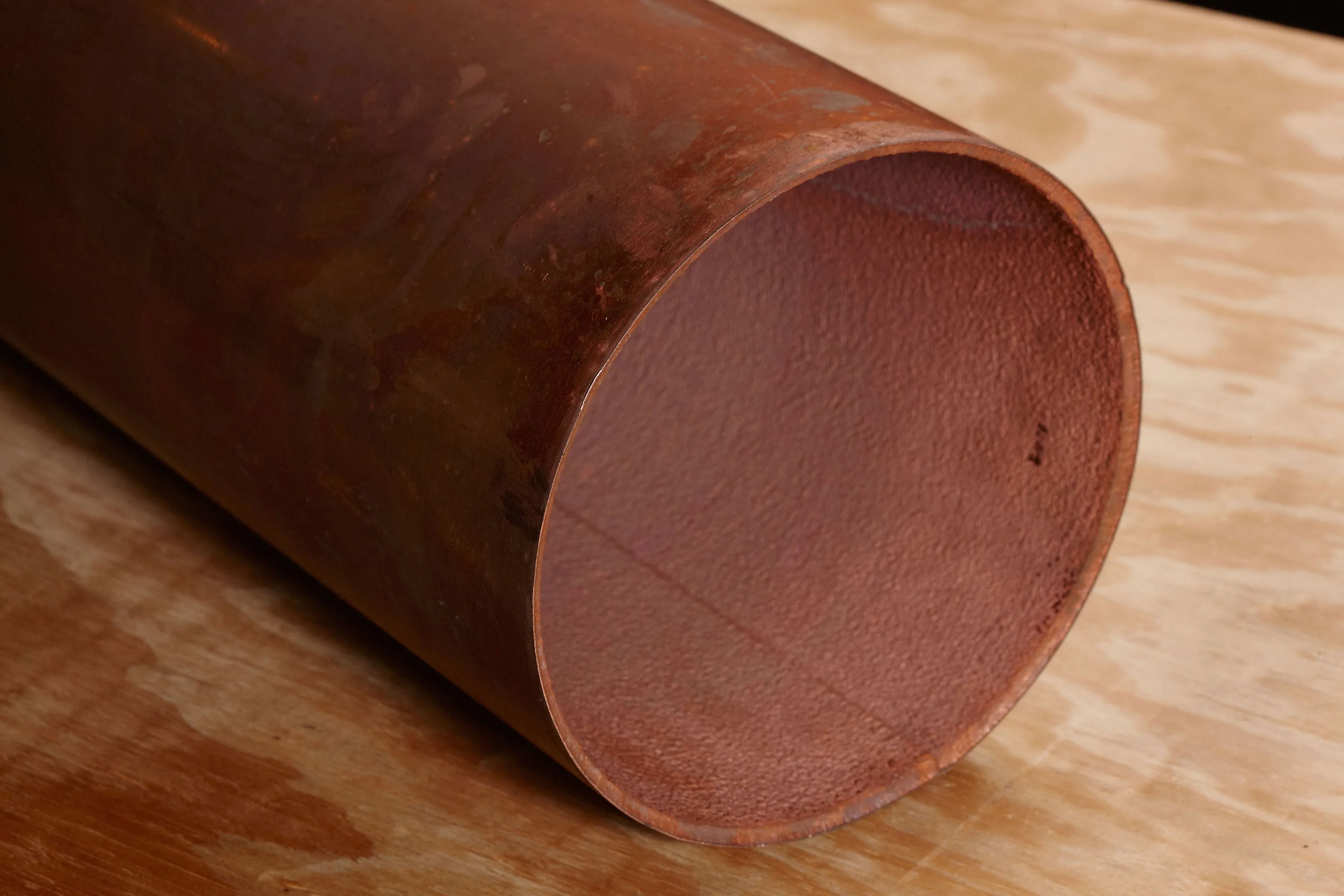
Result:
Running since 2006, emew’s closed loop system achieved:
- Saving $1–$1.5 million annually
- 87% reduction in CO2 emissions vs. mined copper and 85% vs. copper sulfate evaporation
- 90% reduction in labor, with two operators replacing 14 operators, two mechanics and three supervisors
- 81% reduction in sulfuric acid consumption
- 27,000 litres of clean water saved per ton of copper produced (11 million liters annually)