La electroextracción es una forma muy conveniente y robusta de recuperar directamente metales disueltos como el cobre, la plata, el oro, el níquel, el cobalto y el estaño de sus estados acuosos en un electrolito en particular. Por lo tanto, cuando hablamos de recuperación de metales, no es sorprendente que tendamos a centrar la mayor parte de nuestra atención en los metales que nos interesan con el objetivo de recuperarlos de la solución. Después de todo, ese es el objetivo del proceso de recuperación de metales. Sin embargo, de lo que se habla con menos frecuencia es de las impurezas que pueden afectar a la recuperación de metales mediante la extracción eléctrica. En esta entrada del blog se identificarán las impurezas que son más perjudiciales y se analizará su efecto en la extracción eléctrica de algunos metales que se suelen recuperar a partir de soluciones acuosas.
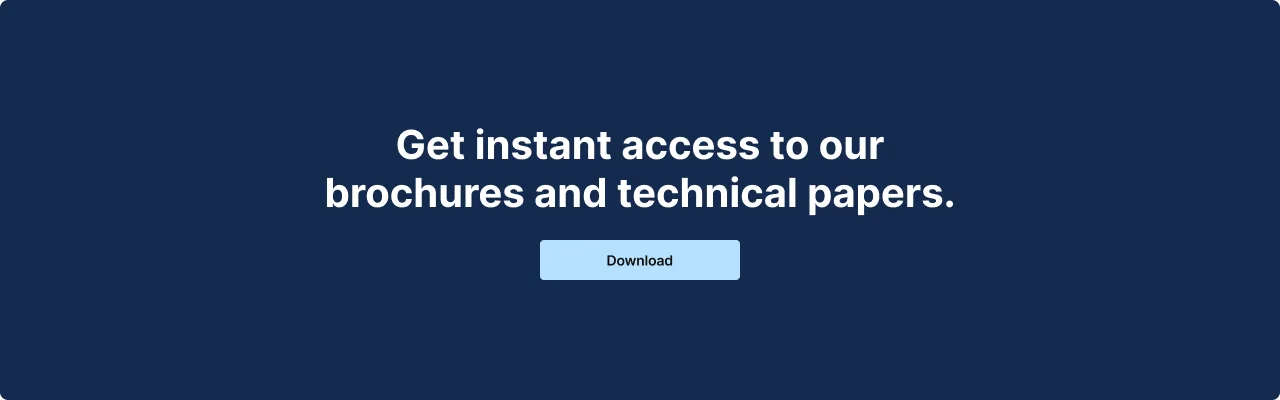
Hierro como hierro (Fe)3+1) Ión
En la recuperación de metales básicos como cobre, níquel, cobalto, y el estaño, así como metales preciosos como el oro y plata, el hierro puede ser una preocupación importante y puede pasarse por alto al considerar la química del proceso. En soluciones acuosas, las especies de hierro oxidado pueden estar presentes en forma ferrosa (Fe)2 o más) y/o férrico (Fe)3+) iones. En una celda electroquímica, el hierro puede ser problemático debido al par redox ferroso/férrico.
En el ánodo, ferroso (Fe2 o más) el ion se oxida a férrico (Fe)3+) ion al perder un electrón (e-):

Mientras tanto, en el cátodo, el hierro (Fe3+) el ion se reduce a ferroso (Fe)2 o más) ion al ganar un electrón:

Si bien estas reacciones parecen equilibrarse entre sí, en realidad consumen electricidad y tienen un efecto perjudicial en la eficiencia actual. La eficiencia actual es la cantidad real de metal recuperado dividida por la cantidad teórica que debería haberse recuperado según la Ley de Faraday. El gasto operativo más importante asociado con la extracción eléctrica es el consumo de energía, por lo que cualquier reacción que compita con la reacción de recuperación del metal primario es indeseable, ya que sirve para reducir la eficiencia de la corriente.
En el caso de la electroextracción de cobre, la reacción preferida en el cátodo es:

Si hay una cantidad significativa de ion férrico presente en la solución junto con el ion cobre, el par redox ferroso/férrico consumirá electricidad y disminuirá la eficiencia de la recuperación de cobre. Por esta razón, como regla general, normalmente recomendamos una relación cobre-férrico superior a seis para garantizar que el par redox ferroso/férrico no consuma electricidad de forma indeseada. Si la relación entre el cobre y el hierro es inferior a seis, puede ser necesaria una etapa de eliminación del hierro, como la precipitación, la extracción con solventes (SX) o el intercambio iónico (IX).
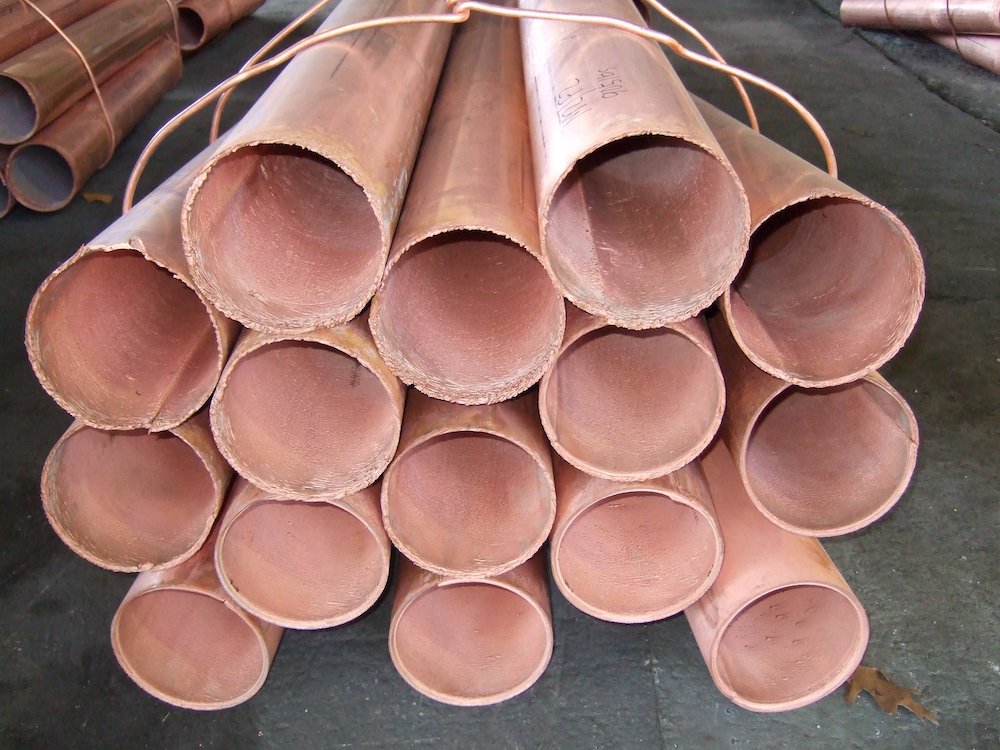
Cloruro
Otra impureza que puede ser muy problemática para la recuperación de metales mediante la extracción eléctrica de soluciones acuosas es el cloruro. El cloruro es una impureza común que se puede encontrar en concentraciones relativamente altas tanto en las materias primas sólidas como acuosas para piensos. El problema del cloruro es doble. Por un lado, el cloruro en sí mismo es corrosivo y corroe las piezas de acero inoxidable mojadas, especialmente en concentraciones superiores a 1 g/L. sistemas de electroobtención, incluido el emew, el cátodo suele estar compuesto de acero inoxidable. En presencia de cloruro, los cátodos de acero inoxidable y otras partes húmedas de acero inoxidable comenzarán a formar pequeños orificios y, con el tiempo, a corroerse hasta el punto de que será necesario reemplazarlos. Esto reduce la vida útil del equipo y contribuye a aumentar los costos de mantenimiento y reemplazo. El otro problema del cloruro es que se oxida en el ánodo y produce cloro gaseoso mediante la siguiente reacción:

El gas cloro es extremadamente tóxico y corrosivo, por lo que es muy importante minimizar la producción de este gas dentro de las celdas de extracción eléctrica durante la recuperación del metal.
Como regla general, normalmente recomendamos mantener los niveles de cloruro por debajo de 50 ppm para minimizar la corrosión y la producción de cloro. En niveles más altos, se pueden usar materiales resistentes a la corrosión, como el titanio, para las piezas húmedas, incluido el cátodo.
Fluoruro y bromuro
Para la recuperación de metales a partir de electrolitos ácidos, sistemas de electroobtención como el emew, utilizan ánodos que desprenden oxígeno compuestos por un sustrato de titanio con un recubrimiento catalítico de óxido metálico mixto (MMO). Estos ánodos de MMO son muy robustos, pero pueden ser particularmente susceptibles a algunas impurezas como el flúor y el bromuro. Como es el caso del gas cloro que forma cloruro, el fluoruro y el bromuro también se oxidan en el ánodo para formar gas flúor y bromo, respectivamente. Estos gases son extremadamente corrosivos y disuelven eficazmente el sustrato de titanio, dejando que el revestimiento de MMO simplemente se desintegre.
Como regla general, normalmente recomendamos mantener los niveles de flúor y bromuro por debajo de 5 ppm para garantizar la máxima longevidad de los ánodos de MMO utilizados en las celdas de electroextracción de energía electromagnética.
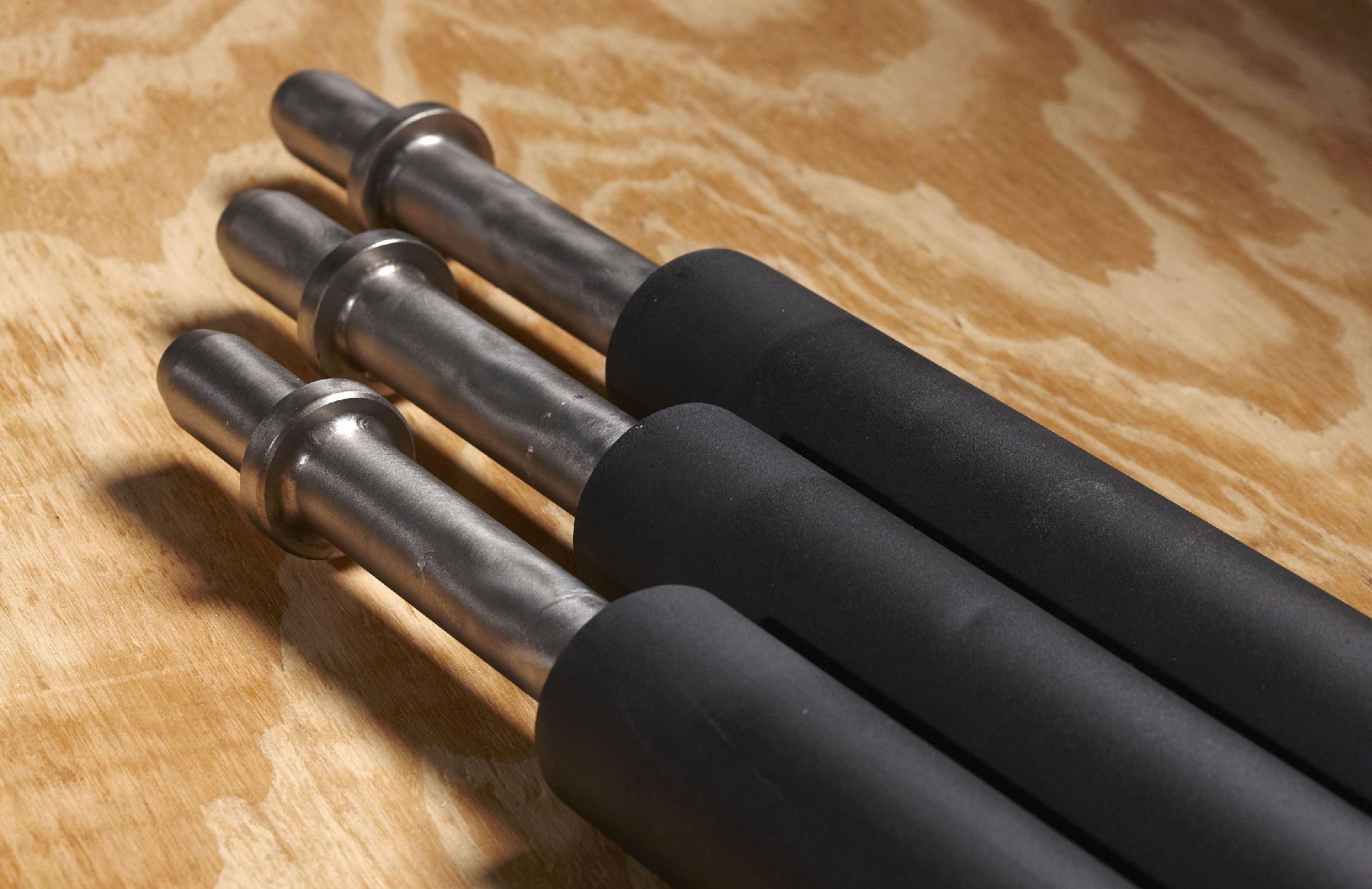
Compuestos orgánicos
Ciertos compuestos orgánicos, como la tiourea, los pegamentos y los surfactantes, también pueden ser problemáticos para los recubrimientos del ánodo del MMO, ya que pueden oxidarse en el ánodo y adherirse al recubrimiento. Esto puede provocar la pasivación y la falla prematura del ánodo. Los agentes quelantes fuertes, como el EDTA, también pueden ser problemáticos, ya que pueden tener una fuerte afinidad por los óxidos de metales preciosos presentes en el recubrimiento de MMO. Si el EDTA se une a los óxidos de metales preciosos, estos pueden desprenderse de la matriz y destruir el revestimiento de MMO.
Si hay compuestos orgánicos en el electrolito, es posible eliminarlos antes de la electroextracción con el uso de carbón activado o pretratamientos similares. Desafortunadamente, estos pueden no ser eficaces para agentes quelantes fuertes como el EDTA, por lo que es importante entender el origen y la química del electrolito a la hora de diseñar un proceso de recuperación de metales.
Resumen
En general, la recuperación de metales mediante la extracción eléctrica es un proceso muy robusto que puede adaptarse a una amplia gama de concentraciones, condiciones de operación e impurezas. Hay un puñado de impurezas que constituyen excepciones notables y se debe prestar atención a ellas al evaluar la aplicabilidad de un proceso de recuperación de metales a un electrolito en particular. Conocer las concentraciones de compuestos férricos, cloruros, fluoruros y orgánicos permitirá adaptar el proceso de recuperación de metales a una matriz de soluciones en particular y garantizar la recuperación efectiva y económica de un metal de interés determinado.
¿Tiene alguna pregunta sobre su proceso de recuperación de metales? Ponte en contacto!