Clean, fresh water is a luxury in many countries and is increasingly becoming a valuable commodity. Our society today is faced with the challenge of harnessing the power of advanced wastewater treatment technologies to preserve our precious water resources. Not only does this apply to municipal water treatment plants that work around the clock to make sure communities all over the world have access to clean, fresh water, but also in industrial processes to minimize usage and waste.
"Presently only 20% of globally produced wastewater receives proper treatment."
- United Nations Educational, Scientific, and Cultural Organization (UNESCO)
In the years following the industrial revolution and continuing on into the information age, industries have been challenged to develop new and innovative ways to treat wastewater and bleed streams to encourage recycling and reduce discharge towards the holy grail of so-called 'zero discharge'. We've come a long way in the latter part of the 20th Century, but there's still work to be done as populations swell, economies grow and everyone strives to improve their quality of life and that of his or her children.
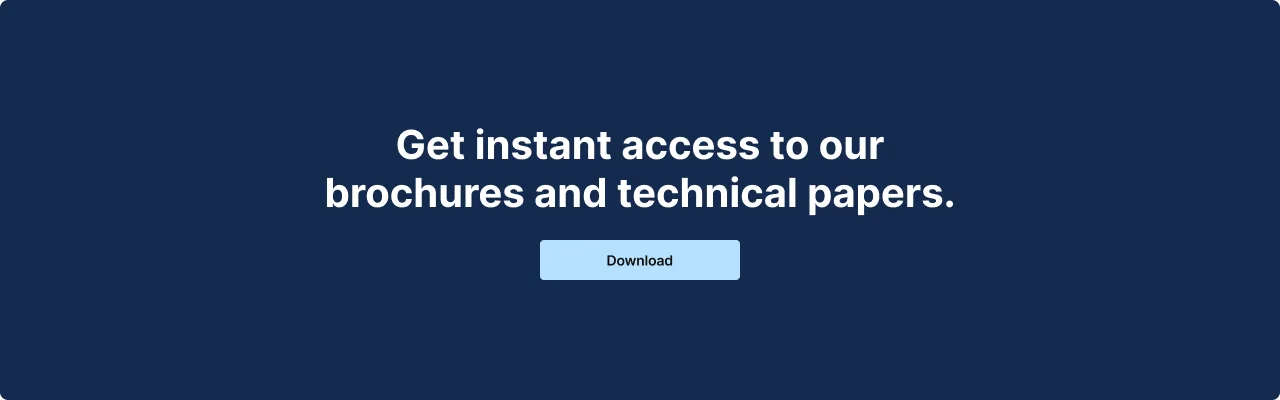
What is wastewater effluent?
Effluent is generally considered to be water pollution. According to Wikipedia effluent is an outflowing of water or gas from a natural body of water, or from a manmade structure. The United States Environmental Protection Agency defines it as "wastewater - treated or untreated - that flows out of a treatment plant, sewer, or industrial outfall. Generally, refers to wastes discharged into surface waters". Wastewater is any water that is affected in quality by human impact on the environment.
The sources of wastewater may vary from municipal and sewage to industrial and agricultural. Sewage is one of the biggest sources of wastewater. Sewage water is contaminated with human waste and makes its way through the pipes, pumps and screens which doesn’t contribute positively to the water quality. Additional sources of wastewater can be wash water that is a result of washing dishes, cars, or clothes. Urban rainfall is considered wastewater as well since it contains oils, rubber and gasoline washed from the streets and building roofs. A large source of wastewater is produced in numerous industrial applications such as metal finishing and plating, chemicals production, mining, refining, pulp and paper manufacturing, oil and gas production and many others.
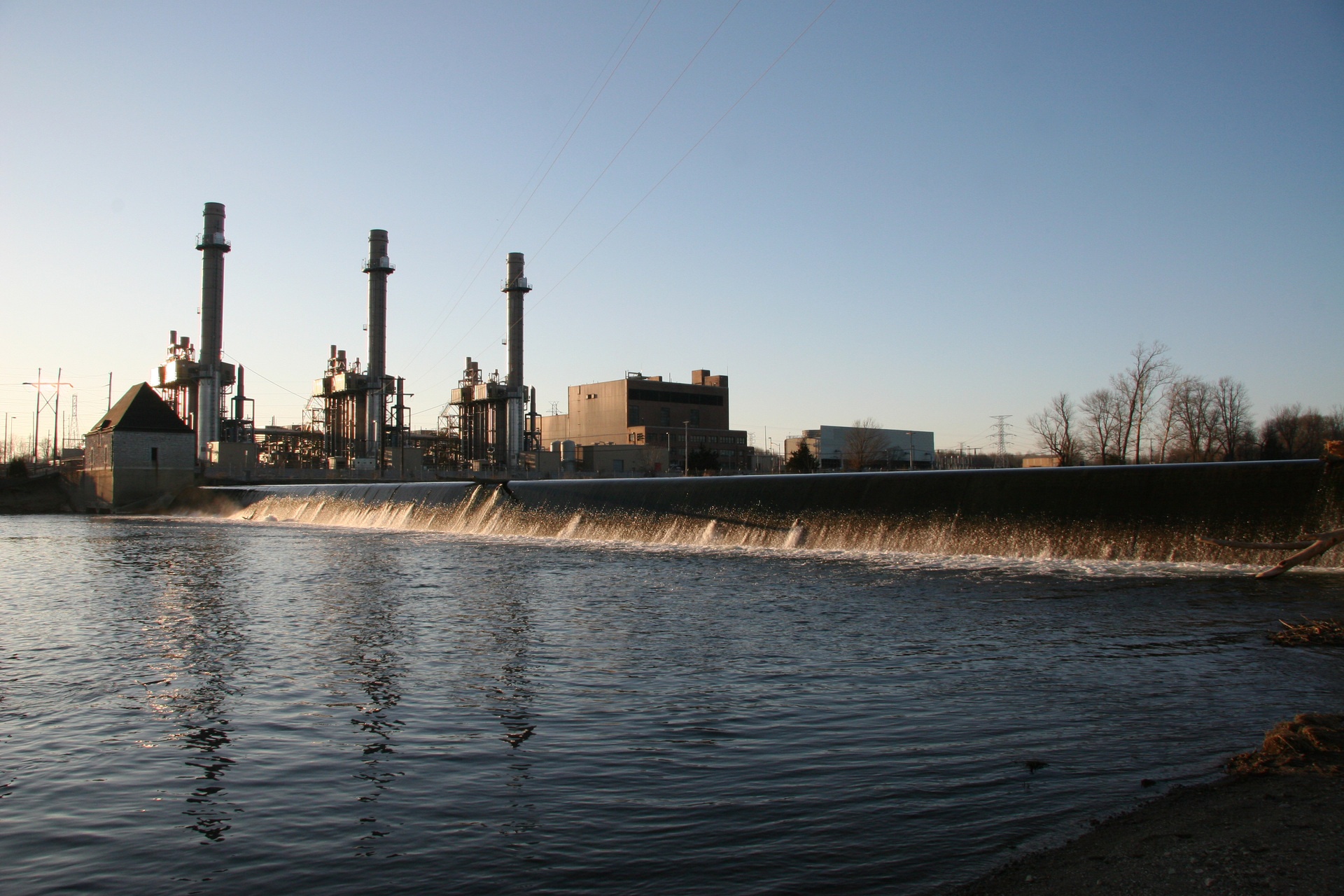
Why is wastewater bad?
The pollutants contained in wastewater have a huge impact on the environment. In many countries all over the world, including Canada and the United States, health issues and diseases are often caused by contaminated water streams that are discharged directly into freshwater pools. The result of such endeavours is pollution, animal and fish fatalities, and human illness. According to the American Academy of Microbiology, 80% of infectious diseases worldwide may be related to water quality and effluent streams disposal. At least 1.8 million children die every year from water-related diseases, one every 20 seconds. We cannot afford to dispose of domestic or industrial wastewater in ways that will affect people’s health and natural environment. Governments are coming to the understanding that wastewater has to be treated and are constantly introducing new regulations that are aimed at monitoring and controlling effluent discharge. Most modern industrial and fabrication operations dispose of their wastewater either using onsite wastewater treatment facilities to treat the water or send offsite to a reputable third party contractor that responsibly treats and disposes of the wastewater. Even with these efforts, only an estimated 20% of all wastewater in the world is properly treated using best available technologies.
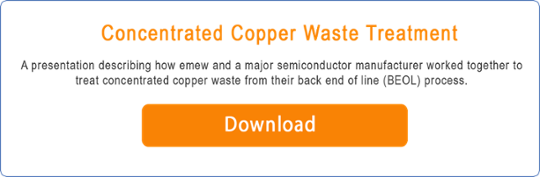
Who regulates wastewater?
In the United States, the Environmental Protection Agency (EPA) enforces the regulations under the Clean Water Act and Safe Drinking Water Act. The main purpose of the EPA is to protect human health and the environment. The organization has the authority to enforce the compliance with environmental regulations and take civil or criminal enforcement actions against violators of the environmental law. The EPA regulates the discharge of pollutants from industrial wastewater plants, as well as sewer collection reservoirs. It is a requirement to pre-treat industrial wastewater inside manufacturing facilities prior to disposal to municipal sewer systems. The oils and metals contained in wastewater damage municipal wastewater plants and lead to a discharge of unwanted pollutants into freshwater pools.
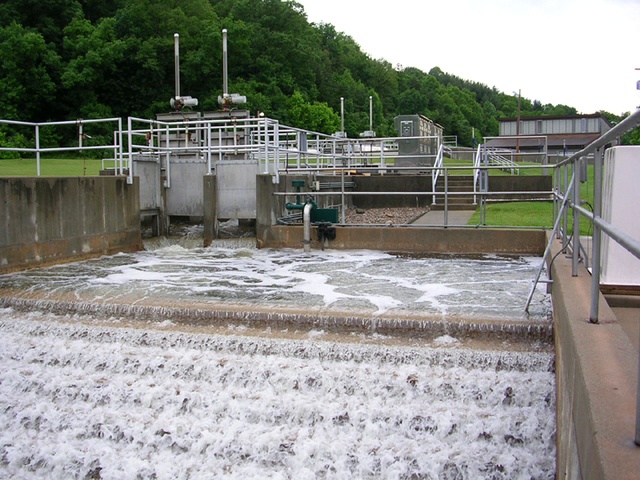
In Canada over 150 billion litres of wastewater that isn't properly treated is dumped into waterways every year. As of January 1st, 2015 Environment and Climate Change Canada introduced the following provisions of the Wastewater System Effluent Regulations:
- The effluent quality standards are set out in Regulations chapter.
- Limits will be enforced effective immediately.
- Monitoring is required for systems that deposit an annual average daily effluent of greater than 2,500 m3 and are not covered by either a transitional or temporary authorization.
Regulatees will be required to submit an electronic report in a format required by Wastewater System Effluent Regulations.
In Europe industrial emissions are regulated by the Industrial Emissions Directive 2010/75/EU which is the main instrument for regulating the emissions from industrial applications. The directive was introduced in 2010 and revised 7 previously existing directives. The directive's purpose is to maintain and improve the level of protection of human health and the environment. It is based on an integrated approach, the use of best available technologies, flexibility, inspection and public participation.
What is a wastewater treatment process?
Wastewater treatment is the process of removing contaminants from wastewater, either from municipal sewage or from industrial applications. These processes are designed to improve the quality of water and meet the standards set for effluent quality. Dedicated and cost-effective wastewater treatment is the key to improving health and environmental sustainability.
How does wastewater treatment help?
There are many ways to reduce pollutants in effluent streams. The process is usually chosen in accordance with the specific effluent and financial considerations. Some of the ways that different effluent treatment processes can remove contaminants:
Municipal wastewater
- Remove solids from the effluent to prevent rivers and sewers from clogging.
- Reduce biodegradable organics and prevent “dead zones” with no fish.
- Reduce pathogenic bacteria and improve the quality of drinking water.
- Reduce nutrients in water as the presence of nutrients increases the amount of a biodegradable organics in the water.
Industrial wastewater
- Remove metals from the effluent.
- Remove oils and other chemicals using adsorption, precipitation or other techniques.
What are some of the processes used to treat wastewater?
Usually, the treatment process will depend on the local regulations of the province, state and country. The goal of any treatment process is to produce an effluent that will cause as little harm as possible and either will be reused in manufacturing or agricultural production or further purified as much as possible prior to discharge. The general trend nowadays is to reduce the generation of wastewater as a result of manufacturing to the minimum. In many industries, however, there is no way around it and wastewater is still produced in large quantities. There are some basic strategies for taking care of contamination.
Brine treatment
Brine treatment is using the same principal as desalination technology which removes the dissolved salt ions from the waste stream. Usually, brine techniques are used to minimize the volume of the discharge for more convenient transportation or to maximize the recovery of fresh water and salt. Brine treatment is widely used in the food production industry and pulp and paper production. In many cases brine treatment is applied through evaporation, producing a salt in high concentration. The disadvantage of brine treatment is high electricity consumption. Brine treatment can be used both in municipal wastewater treatment applications and to treat industrial wastewater.
Solids removal
This method is used to remove solids in the form of a slurry from the water and usually done with sedimentation techniques. In many cases, flocculation is used to aid in the collection and sedimentation of fine solids.
Oils and Grease removal
There are various ways to tackle oils and grease. Since there are few different types of oil pollution states possible, the technique for wastewater treatment is chosen according to the type of contamination.
The most common type of oil pollution is emulsified. Oil droplets are heavily chopped and usually are very difficult to treat. Generally, the larger the droplets – the easier to remove from water. Additional possible states of oil pollution are:
- Free Oil – In this case, the droplets are large and sitting on the surface of the water, which is the easiest state to deal with. Since the density of oil is much higher than of water, the oil floats on top of the water and can be easily collected.
- Heavy Oil – oil that has a muddy structure and sits at the bottom of the water.
- Dissolved Oil – the size of oil droplets is very small and mixes well with water.
Electrolysis
Electrolysis is widely used in chemical and manufacturing applications. By applying a direct current (DC) to an ionic substance (electrolyte) it is possible to separate the materials contained in the solution. The ions that discharged during the process are plated onto the cathode and harvested after some time reducing the concentration of pollutants in solution. The length of treatment and voltage is determined based on a concentration of pollutants in solution and type of pollutant. Electrowinning technology is based on electrolysis and used to recover metals from contaminated water streams.
How can industries improve wastewater treatment processes?
Most people are now familiar with the 3R's of recycling: Reduce, Reuse, Recycle. By following four similar principles: Recover, Reduce, Recycle and Rescue, industries can further minimize raw resource requirements, eliminate waste disposal fees and increase margins all while promoting circular economies. Let's take a look at these four R's.
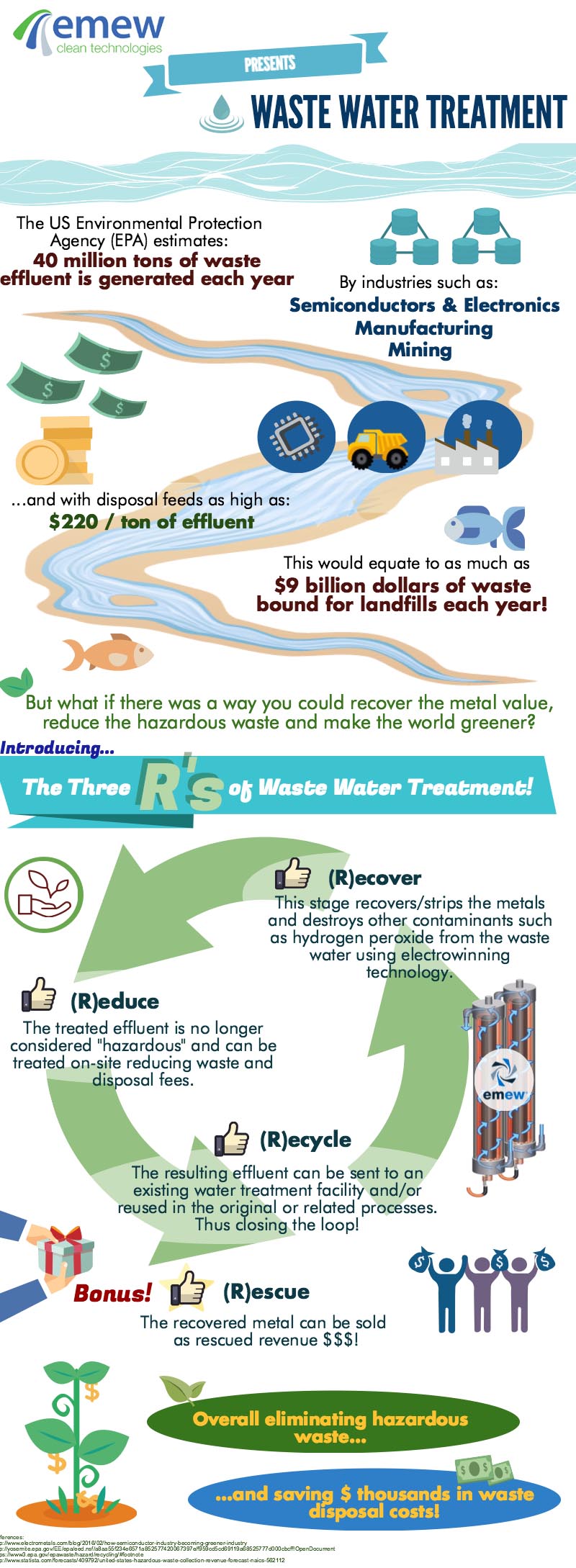
Recover
During any given manufacturing process, wastewater is often generated along with the finished product. The wastewater can have a myriad of components that can include inorganics, organics, base and/or precious metals. In some cases, a certified hazardous waste disposal contractor is hired to remove the wastewater for treatment offsite. Often the sludge generated from the treatment of so-called hazardous waste is deposited in secure, monitored landfills if it cannot be reused or recycled. Metal hydroxides generated from pH adjustment using caustic or lime precipitation are not generally wanted by smelters and other metallurgical facilities as they are endothermic, difficult to process and often contain the periodic table from A-Z.
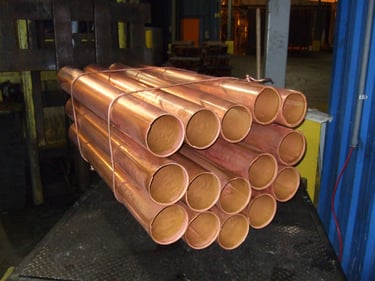
Reduce
Most modern industrial facilities have onsite wastewater treatment plants to treat the bulk of the wastewater. Sometimes wastewater from certain processes has contaminants that prevent it from being treated with the bulk. In this case, the wastewater may be segregated for processing offsite so as not to compromise the efficiency and efficacy of the existing wastewater treatment plant. What often goes unnoticed, is that by just recovering some of the metals and/or destroying some of the contaminants in the wastewater in a dedicated pre-treatment system, the resulting effluent can be processed within an existing on-site bulk wastewater treatment facility. The result is a reduction in hazardous waste bound for landfill not to mention saving the offsite treatment costs.
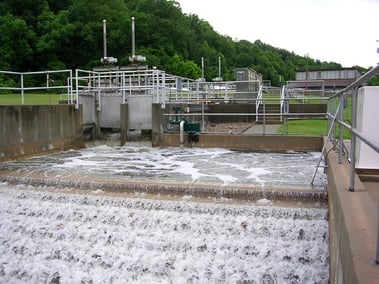
Recycle
Metals are endlessly recyclable. By recovering metals from wastewater in a pure form, they can be recycled within the manufacturing process or sold to generate revenue to offset treatment costs. Furthermore, treating so-called 'bleed streams' in this way allows for the recycling of the effluent decreasing the need for fresh water and chemicals such as acid, caustic, etc. This holistic recycle of metals, chemicals and water promote the ultimate closed loop 'zero discharge' process that is the holy grail of industrial processing.
Rescue
Wastewater treatment comes at a cost - and the more complex the treatment requirements, generally the higher the cost. But what if the process of wastewater treatment actually generated a saleable product? A holistic approach to preserving and managing natural resources in industrial processes can rescue revenue by recovering and recycling metals, chemicals and water. Metals recovered as high purity cathode can be recycled or sold to the market overall adding value to what was once considered valueless!
Wastewater treatment with emew
In a conventional electrowinning process, the anode and cathode are placed in a bath with a solution which is either stagnant or slowly circulating. The direct current (DC) applied to the anode causes plating of the metal ions onto the cathode through diffusion. After some time, the depletion of the metal will significantly decrease and the purity of the metal will be affected if there are other contaminants in the electrolyte.
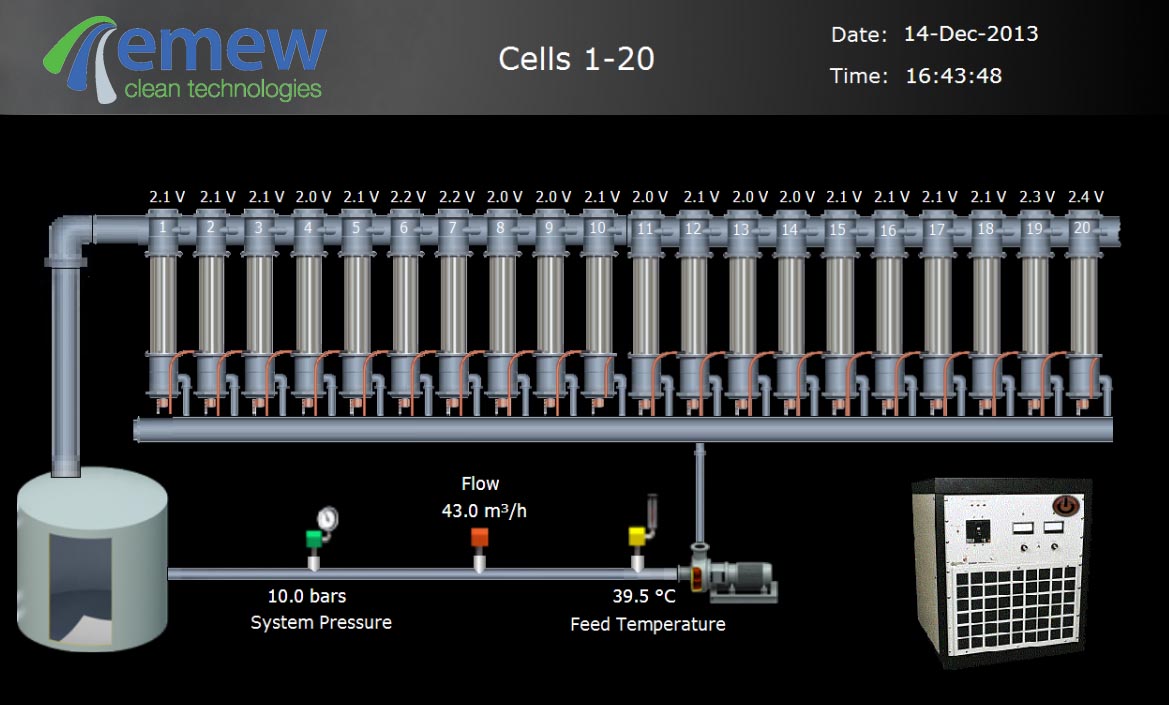
With emew electrowinning, the solution is rapidly circulating through the enclosed cell eliminating depletion zones and improving the purity of recovered metals. Each emew cell consists of 150mm-200mm diameter cylinder made of stainless steel. The anode runs through the centre of the tube and the inner surface of the tube plays the role of the cathode. While the solution is flowing from the bottom to the top of the cell, DC voltage is applied in order to create an electrical potential difference between the anode and cathode. After the desired hours of plating, the metal can be harvested from the cell.
There are many benefits of using emew technology:
- Higher purity, improved recovery, increased efficiency and lower operating costs.
- Maintenance and support services to maximize uptime and optimize operational performance.
- Customized technology packages including outright purchase, plant rentals, and metal-as-a-service arrangements.
- Confirm process design and operating parameters with laboratory test programs, pilot/demo programs, flowsheet and general process development services, as well as feasibility studies.
- Uncompromised safety and environmental performance for personnel and operations.
Safety Improvements with emew:
emew electrowinning has set a whole new standard to safety when it comes to wastewater treatment.
In conventional electrowinning bubbles of air are produced at the anode. When these bubbles reach the surface of the anode they burst and release sulfuric acid (acid mist) into the air. Acid mist is an extremely hazardous material which presents a danger to employees and visitors of the facility. In addition to this, the acid mist is very corrosive and significantly reduces the lifetime of plant parts.
The advanced emew electrowinning cells designed to eliminate the presence of acid mist, which makes for a safer work environment. The emew plant is completely enclosed and all gases are contained within the system. It doesn’t require additional ventilation and creates a new standard in health, safety and environmental (HSE) performance.
Semiconductor wastewater treatment with emew
About 10 years ago, Copper replaced Aluminum for the back end of line (BEOL) interconnects in the semiconductor industry. This was due mainly because of some key features of Copper compared to their Aluminum counterparts:
- lower resistance,
- lower power consumption,
- better conductivity,
- better for smaller structures,
- less need for tungsten interconnects (simpler process)
The downside of using copper for improved semiconductor performance is that it created a copper-rich effluent from electroplating that is considered hazardous waste. This copper-rich waste stream also contains high levels of hydrogen peroxide that in most cases cannot be treated on site using conventional effluent treatment processes. The result is that most semiconductor manufacturers resort to having a certified waste contractor take and treat the plating solutions offsite. All companies have a social and ethical responsibility to treat wastes generated by their operations using best available technologies (BAT) and most take this very seriously.
To that end, to ship hazardous material offsite is not considered an environmentally sustainable practice and moreover, it has a considerable financial implication to their bottom line. Semiconductor manufacturers like Samsung, Intel and others are keen to invest in green technologies that enable them to treat hazardous wastes onsite in order to achieve their strict sustainability and environmental objectives.
Fortunately, many semiconductor manufacturers have taken the initiative to utilize metal recovery techniques such as electrowinning to quantitatively remove the copper and destroy the hydrogen peroxide, in other words, waste water treatment. Electrowinning has been used in the mining and metals industry for over a century but is now being embraced by the hi-tech industry as well. The result is an effluent that can now be easily treated by their existing effluent treatment facility.
Not only does this eliminate the increasingly expensive disposal fees of copper liquid waste, but also produces saleable copper as additional revenue or recycle.
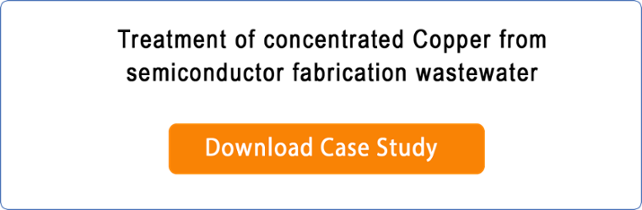
While the amount of saleable copper generated does not justify the capital expenditure of a new electrowinning process, the hundreds of thousands of dollars saved from paying waste disposal contractors to treat the waste more than justifies the investment. In most cases, the financial payback can be 6-12 months while the sustainability and good karma last forever.
In one example, by investing in a small custom design electrowinning plant to treat copper plating waste, a leading semiconductor manufacturer achieved:
- a return on investment (ROI) within 12 months,
- produced up to 60,000 lbs of saleable copper a year, an
- …reduced their hazardous copper waste shipments by 1 million gallons a year!
Certainly, examples such as this one clearly show that the semiconductor industry is leading by example by embracing green technologies to overcome environmental, technical and financial challenges.
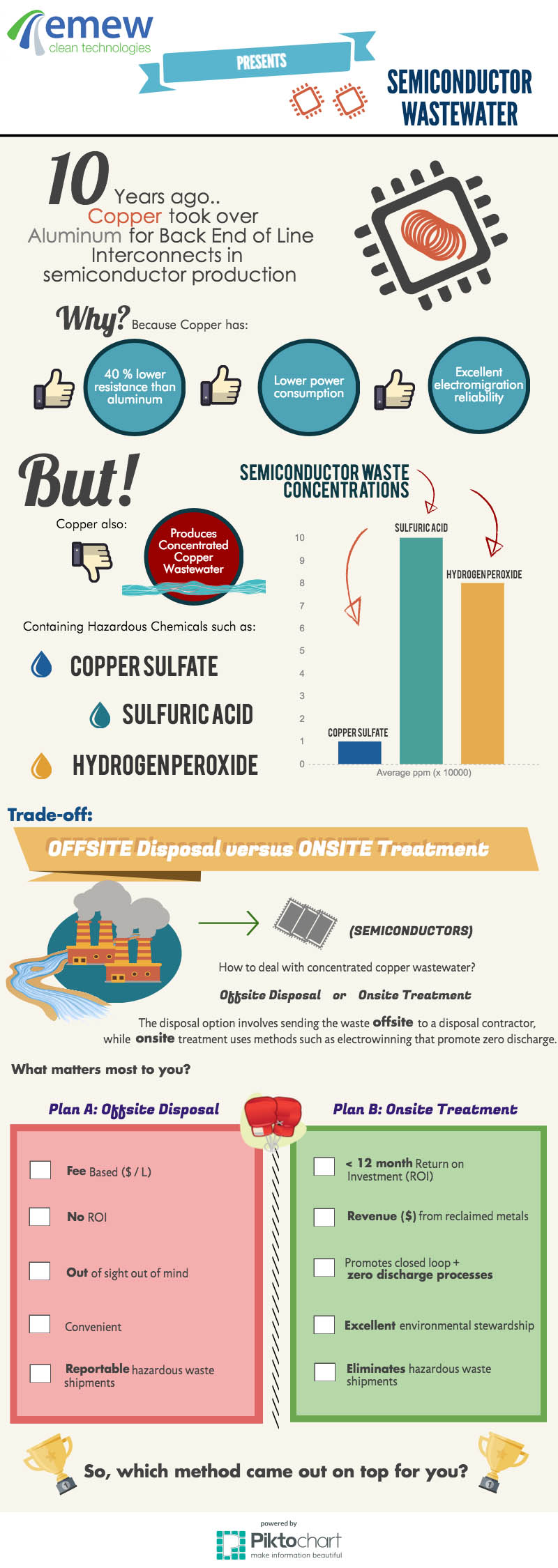
And What About Mine Waters?
As copper continues to be a rich and desired resource for a variety of products such as electrical wire, building infrastructure, electronics and other technology alike, copper process plants have responded by striving to continuously optimize and capture as much copper as possible from their mining processes.
Mining processes have always looked for different ways to optimize their operations such as saving water, using less energy, and minimize on-site waste streams or tailings. Some of these optimizing techniques have included process water recycling from clarified tailings, transferring energy between solutions in heat exchangers, incorporating more gravity controlled flows between processes instead of using pumps, or recovering lost metal from waste streams.
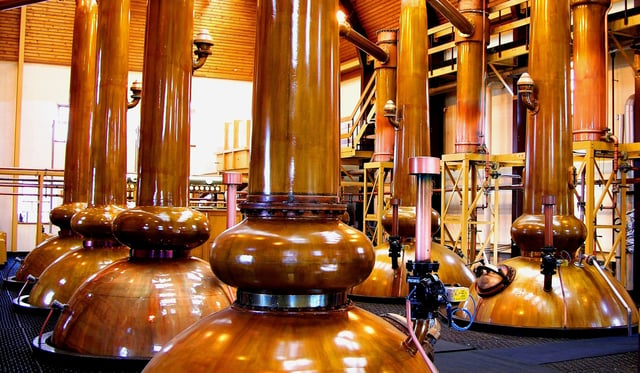
In particular, copper mines today use a wide variety of complex process designs which take high and low-grade ore to produce many tonnes of concentrated copper for further refining before it is available for consumer use. These include mineral processing techniques such as solvent-extraction (SX) for low-grade ore; and crushing, grinding and froth flotation for high-grade ore. In addition to these primary copper processes, copper plants also face copper-containing waste streams derived from these processes and acid mine drainage (AMD) the result in the loss of significant amounts of valuable copper inhibiting the full efficiency of production.
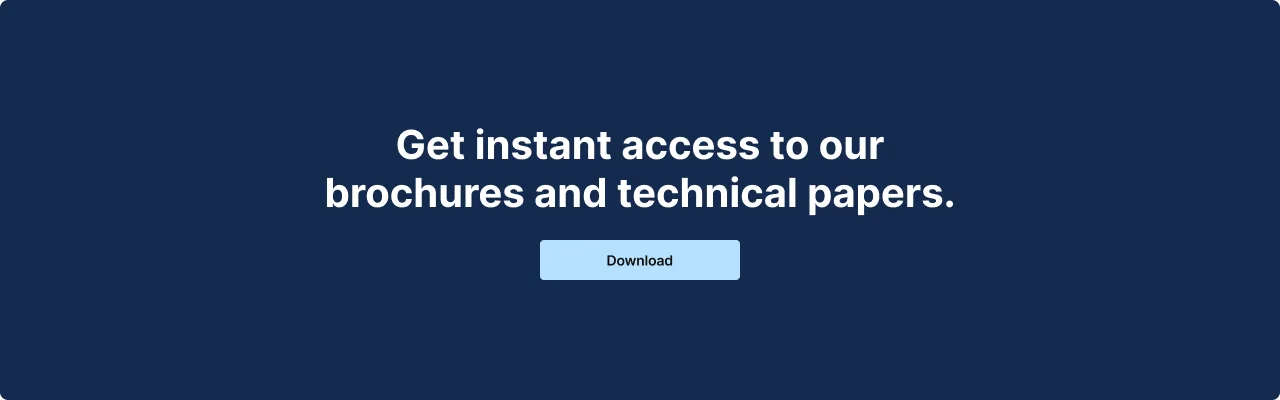
Within these copper mine operations, the low grade run-of-mine (ROM) material is leached using sulphuric acid to produce copper-containing pregnant leach solution (PLS) that is then processed through by SX producing two streams: a concentrated copper-rich electrolyte and a copper-barren raffinate which is neutralised with lime before being sent to the tailings area where clarified water is recycled in the mining process as process water. Even though the raffinate is considered "copper-barren" it may still report copper concentrations not captured in the concentrated stream. With large volumes of raffinate flowing per hour, hundreds to upwards of thousands of tonnes of copper per year can be lost within a single waste stream.
Meanwhile, in the higher grade ore processes, the thickener and filters process the copper from the flotation circuits where it is further concentrated leaving overflow and filtrate as process water with varying degrees of copper left to be used as process water or direct to tailings. Naturally, process water will mix with other surrounding waters like pit or stormwater eventually collecting together and running off to nearby water areas generating acid mine drainage containing traces of copper that can also be lost from normal operating productions.
Is there an effective technique for mining operators to recover these copper units from low-grade process water such as raffinate and AMD? Let's take a look at one technique that has been commonly used in other industries and now gaining more interest in mining applications as operators strive to recover more copper, reduce waste and meet their sustainability challenges.
Ion-exchange (IX) and electrowinning
One common and effective technique used in the waste-water treatment industry is ion-exchange (IX), a process which involves a column filled with specific grades of resin designed to selectively load particular metal ions from the passing solution, resulting in a metal-ion-rich loaded resin and a metal-ion-barren stream that's sent through to disposal or other means.
In the case of copper plants with copper waste streams, resins with higher selectivity for copper are used. These types of resins often have a scale of selectivity allowing to effectively load copper onto the resin away from other undesired species such as calcium or magnesium.
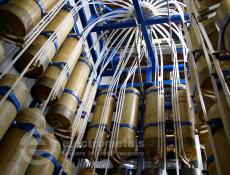
Oftentimes, iron is also present in these copper solutions and may limit pure copper loading since iron may be higher in selectivity than copper. Fortunately, by loading copper onto the resin at a certain pH, iron can be removed from the solution as a precipitate overall minimizing iron loading and interfering with high purity copper loading, onto the resin.
A typical industrial set-up of IX starts off as a fixed-bed process with two working IX resin filled columns for copper loading, and a third elution column used for stripping the copper from the resin out. The feed stream is first pumped into the first two IX columns to absorb the copper from the solution before exiting as a copper-barren stream. The first IX column is taken offline to have sulphuric acid (H2SO4) pass through to strip the copper producing a copper sulphate (CuSO4) electrolytic stream from the resin.
This copper sulphate stream is then introduced into an electrowinning process, most conventionally with a tank and two opposing electrodes known as an anode and a cathode, and passing current through the electrolytic solution. This electrowinning process recovers the copper in solution and plates it onto the cathode forming a high purity metal copper product.
The resulting copper metal from the electrowinning process is harvested once the solution reaches a depletion limit as a high purity solid metal and can be sold to market overall recovering copper plant production revenue that was once left in the tailings and regarded as waste.
Related: Electrowinning 101 - What is electrowinning?
emew after IX
Where electrowinning is concerned, copper can be very effectively recovered from solution by emew's unique method of accelerating the contact rate of copper ions by cycling electrolytic solution through a cylindrical cathode and centralized anode. This increase in contact increases the rate of recovery and current efficiency generating more copper per cycle than any other conventional electrowinning processes.
Combining the IX eluate high concentration copper sulphate solution and processing it through emew does not only manage the copper waste solutions but also effectively increase overall copper production revenue as well as offer advantages to the long-term environmental challenges of acid mine drainage. Since emew can operate at much lower concentrations than conventional electrowinning, the upstream IX system only needs to produce an eluate with 10 g/L copper which has implications on the size, capex and opex of the IX equipment and resin. This makes emew an ideal partner to IX for treating low-grade mine waters such as raffinate and AMD.
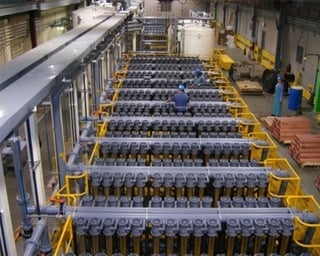
Environmental benefits in mining
Environmental sustainability is considered at every stage of the mining process, and even more so during production and afterwards when the mine eventually closes. More often than not, even if all copper operations cease, AMD will still occur. Typically these waste streams are treated by lime addition to increase the pH and precipitate the dissolved copper and other solubles before collecting as a sludge in a dedicated tailings pond.
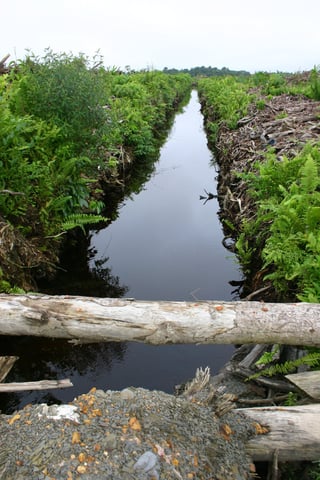
As a result of processing the waste streams with IX and electrowinning and recovering copper, thousands of tonnes of sludge is diverted for copper recovery while also minimizing the total volume sent to tailings. Ultimately, the reduction of waste streams minimizes the long-term AMD impacts to the surrounding environment such as rivers, reservoirs and other wildlife areas.
How do the economics look? Addressing the financials... a case study:
A copper mine having a low-grade waste stream with approximately 125ppm copper and nominal flow rate of 1000 m3/h would have around 1000 tonnes of copper a year that could be recovered. A financial breakdown of each component required to operate an emewIX operation is integral to show annual economic benefits for the project.
Let's take a closer look ...
Both IX and emew have one-time capital costs for the equipment and installation as well as ongoing operating costs such as labour, power, and consumables such as acid and resin. Using IX capital and operating costs estimated in the "Recovery of copper from Chilean mine wastewaters" by Kathryn Sole (2016), the capital and operating costs for a 930 t/a copper IX plant are estimated to be around $5M and $1.7k per tonne Cu produced.
An emew plant capable of 1000 t/a copper production would have a capex of $2.5M (roughly 50% of the IX system) and operating costs of approximately $400 per tonne copper assuming a 5-year LOM.
Ion-exchange (IX) $ Capital costs, $M 5.3 Operating costs, $/t Cu1730 emew $ Capital costs, $M 2.5 Operating costs, $/t Cu 400 Project Economics $ Copper price, $/t4500 Revenue (after deductions), $M/a2.3 Payback period, years< 3.5
* Estimate used a recovery rate of approximately 95% of total available copper, operations running at 97% of the year (355 days), and power consumption of 3 kW / kg of Cu at a price of $0.07 / kWh.
Operating costs for both IX and emew stem from consumables, labour, and maintenance to keep the processes operational throughout the year. These include:
- Resin replacement
- Sulphuric acid replenishment
- Power consumption
- Labour
- Maintenance
As described in the earlier sections, the resin and sulphuric acid may regenerate approximately 90% of original strength and can be reused with minimal fresh resin or sulphuric acid replenishment.
Power is limited to pumping the copper solutions, control systems and of course the rectifier to provide current for electrowinning the metal.
Labour requirements for emew are approximately 1 person-hour per tonne of copper as operators are only required for harvesting with minimal process supervision. Furthermore, the acid mist is completely eliminated with emew since it involves a closed cell design keeping carcinogenic acid mist out of the operators' workplace.
Regular preventative maintenance is essential to keep process equipment and parts running as smooth as possible ensuring optimal efficiency and production throughput.
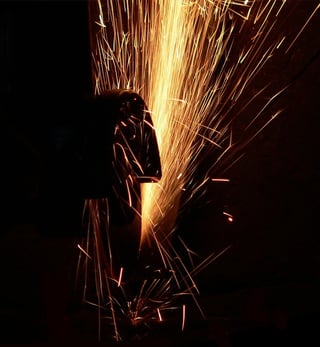
Where a copper mine once had low-grade waste streams and lost copper units, by implementing an emewIX system, this lost revenue can be recovered while promoting waste minimization and operational efficiencies.
Combining IX and emew capital and operating costs for 1000 t/a copper production would generate over $2M after deductions worth of previously unrealized copper revenue that was once left as waste. A payback of fewer than 3.5 years is estimated after including initial capital and deductions from operating costs, optimizing copper productions and financials as well as improving common copper mine environmental concerns.
The emew IX advantage(s)
By coupling tried and true IX and emew together into a 1-2 step solution for copper mine waste solutions, many benefits can be realized for copper mines looking for incremental copper production, improved cash flows, and reduced environmental footprints. In particular, implementing emewIX offers:
- Increase annual salable copper production
- Process optimization resulting in lower working capital
- Recovering copper revenue previously lost to tailings or sludge
- Decreasing environmental footprint and legacy liabilities
- Quick payback on a project that can remain operational after mine closure to treat AMD
With copper mines looking for every opportunity to increase production and decrease costs while improving safety and environmental performance, treating low-grade copper waste streams with systems such as emewIX could very well be the ticket to the next pinnacle of operational success.
Conclusion
Just in North America close to 85 cubic kilometres of wastewater is generated each year. 75% of this water is treated, however, just 3.8% of that treated water is reused. Is this something we can continue on into the future considering the scarcity of clean, fresh water resources available? And what happens to the untreated 25% of wastewater, where does it go? Well, it ends up in our rivers, lakes and underground freshwater streams.
Technology like emew electrowinning allows companies to recover metals from wastewater and reuse the treated water within their existing process. The emew cell can recover copper, nickel, tin, silver, platinum, cadmium, cobalt and a variety of other metals. While minimizing operating costs and environmental impact emew eliminates hazardous waste turning wastewater into water. With emew, it is possible to destroy hazardous components such as hydrogen peroxide and ammonia, reduce waste bound for landfills by recovering saleable metals, and ultimately help companies achieve their most stringent environmental targets and sustainability objectives.