The Coming Copper Crunch
Global demand for copper is on track to double by 2040, driven by electric vehicles, renewable power, electronics and other uses. If this happens, the supply-demand gap will likely increase to the equivalent of today’s total mine production. Recycled copper will be required to help close this gap. Recycling of Printed-Circuit boards (PCBs) can help close that gap as they contain 15 – 30 % copper by weight, yet much of this metal still ends up in landfills or low-value processing routes. Recovering copper efficiently isn’t just good housekeeping - it unlocks better gold yields.
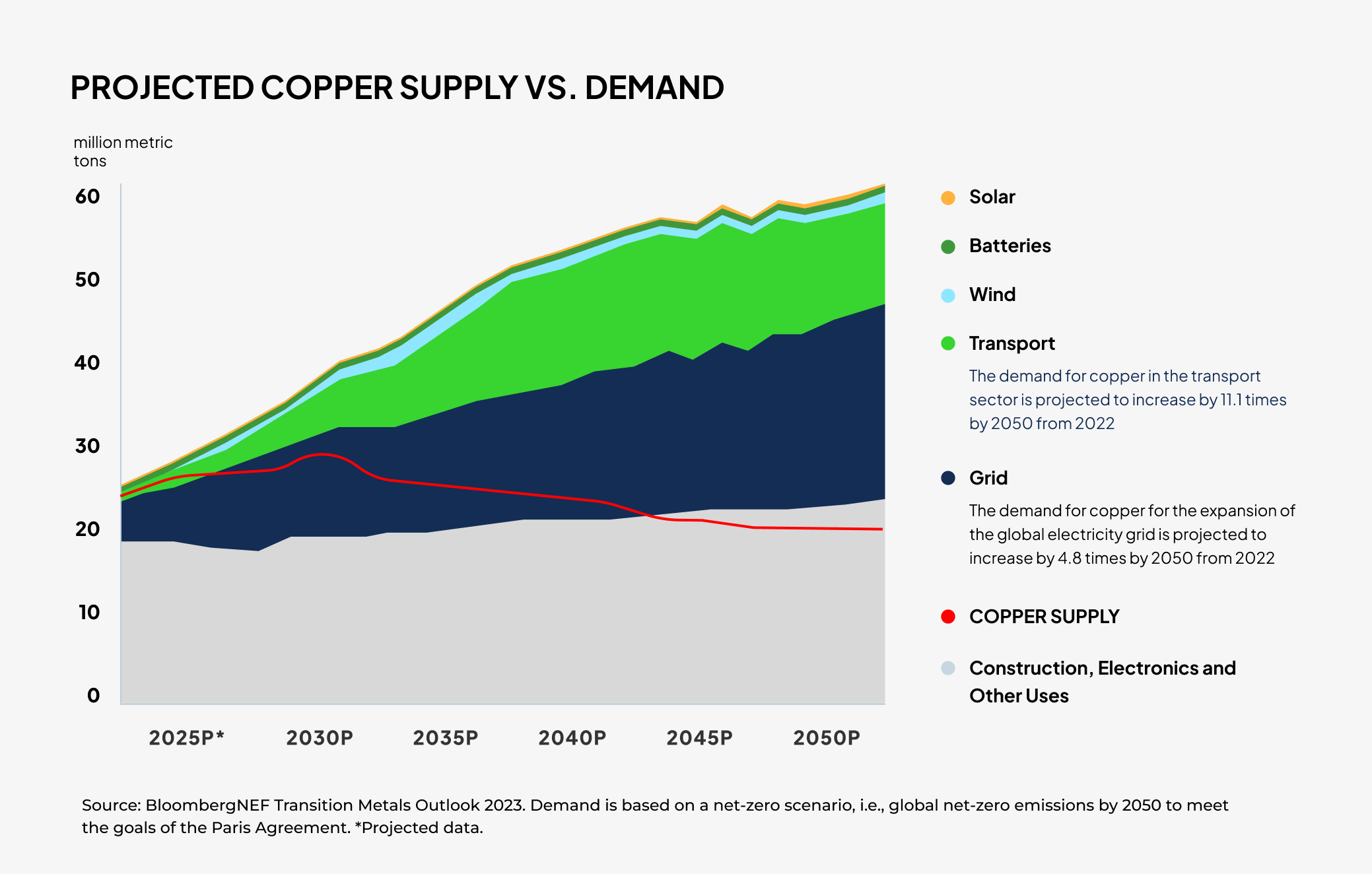
Before the Pandemic: “Ship &Smelt”
Until recently, the dominant model was simple: dismantle and shred e-waste, pack it in containers, and send concentrates to a handful of centralized smelters. Most of those smelters rely on copper electro-refining, with only a few running leach-and-electrowin circuits to accelerate precious-metal liberation. The system works at scale but brings long payment cycles, non-homogeneous materials with difficult metal balances, and a higher carbon footprint than localized processing.
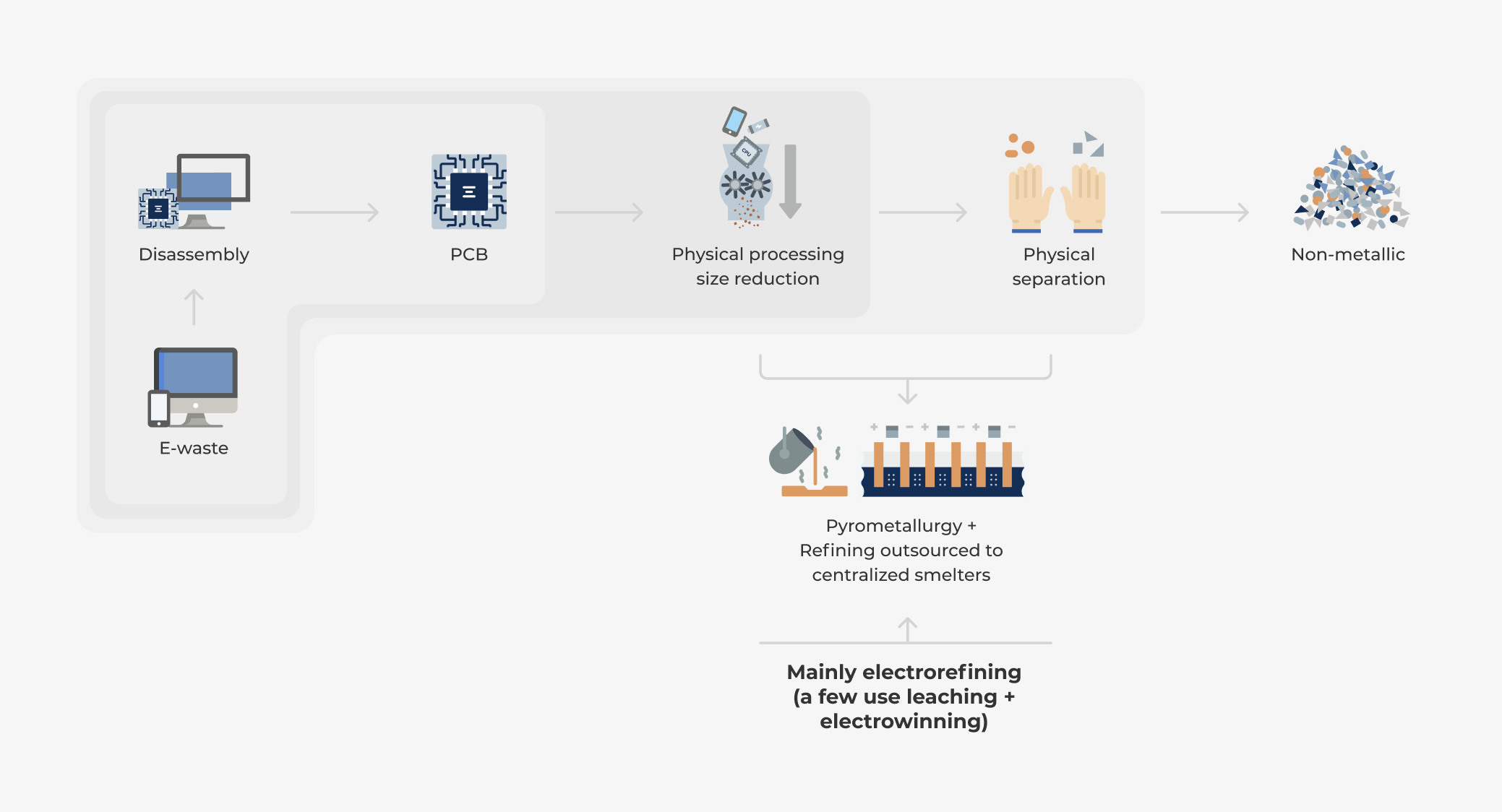
COVID-19: A Shock That Changed theEquation
Lockdowns, soaring freight costs, and border restrictions forced recyclers to rethink distance-based refining. Small collectors struggled with six-month settlement times, while OEMs and governments started prioritizing resource security. The result? A surge of interest in localized refining flowsheets.
The Rise of Local Alternatives
From Australia’s Sircel to Aurubis in the United States, a growing map of regional refiners complements traditional smelters, helping reduce freight carbon footprint.
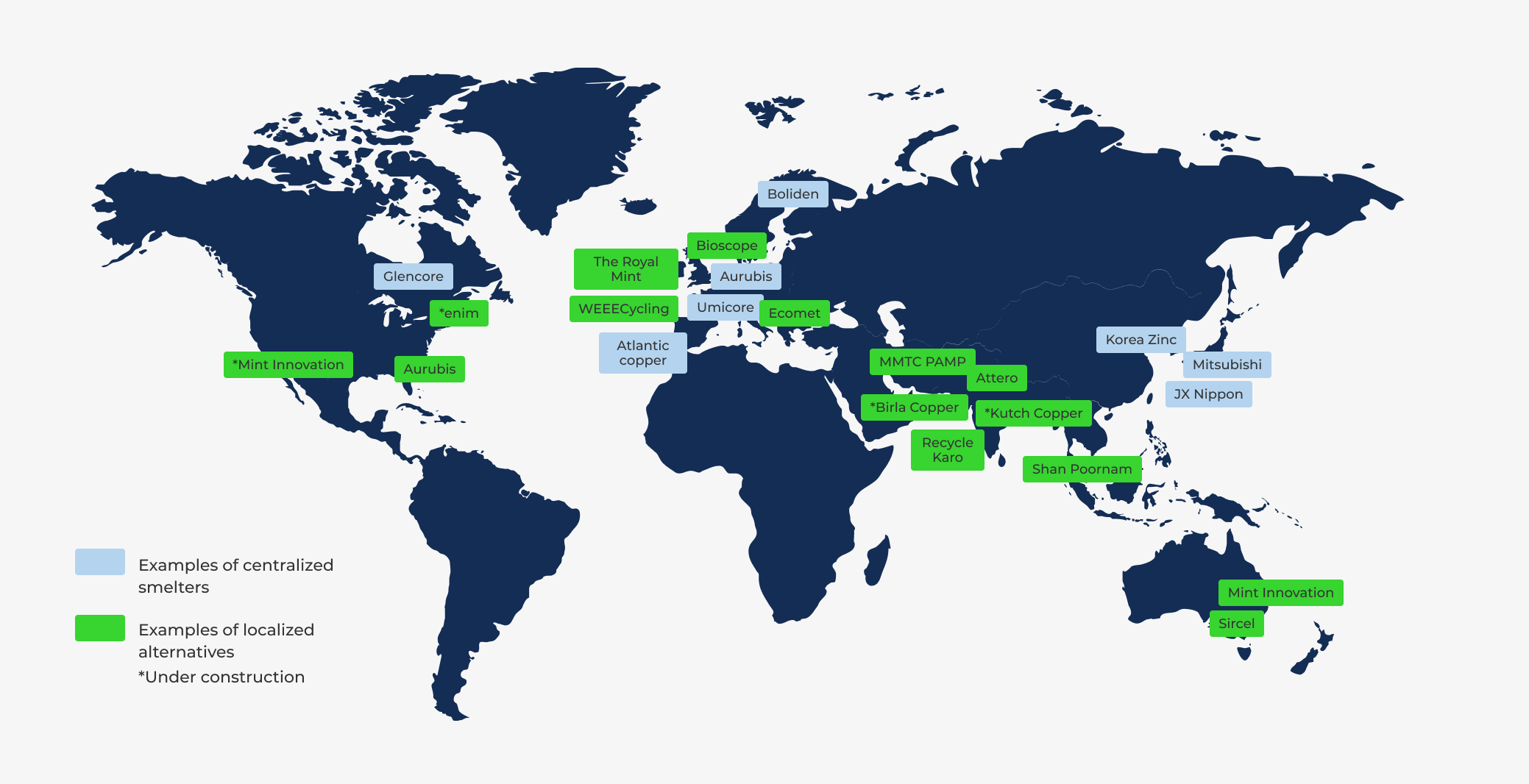
Post-COVID value chains increasingly split e-waste streams: high-grade material to smelters, and mid-grade or mixed batches refined locally via leach-and-electrowin circuits.
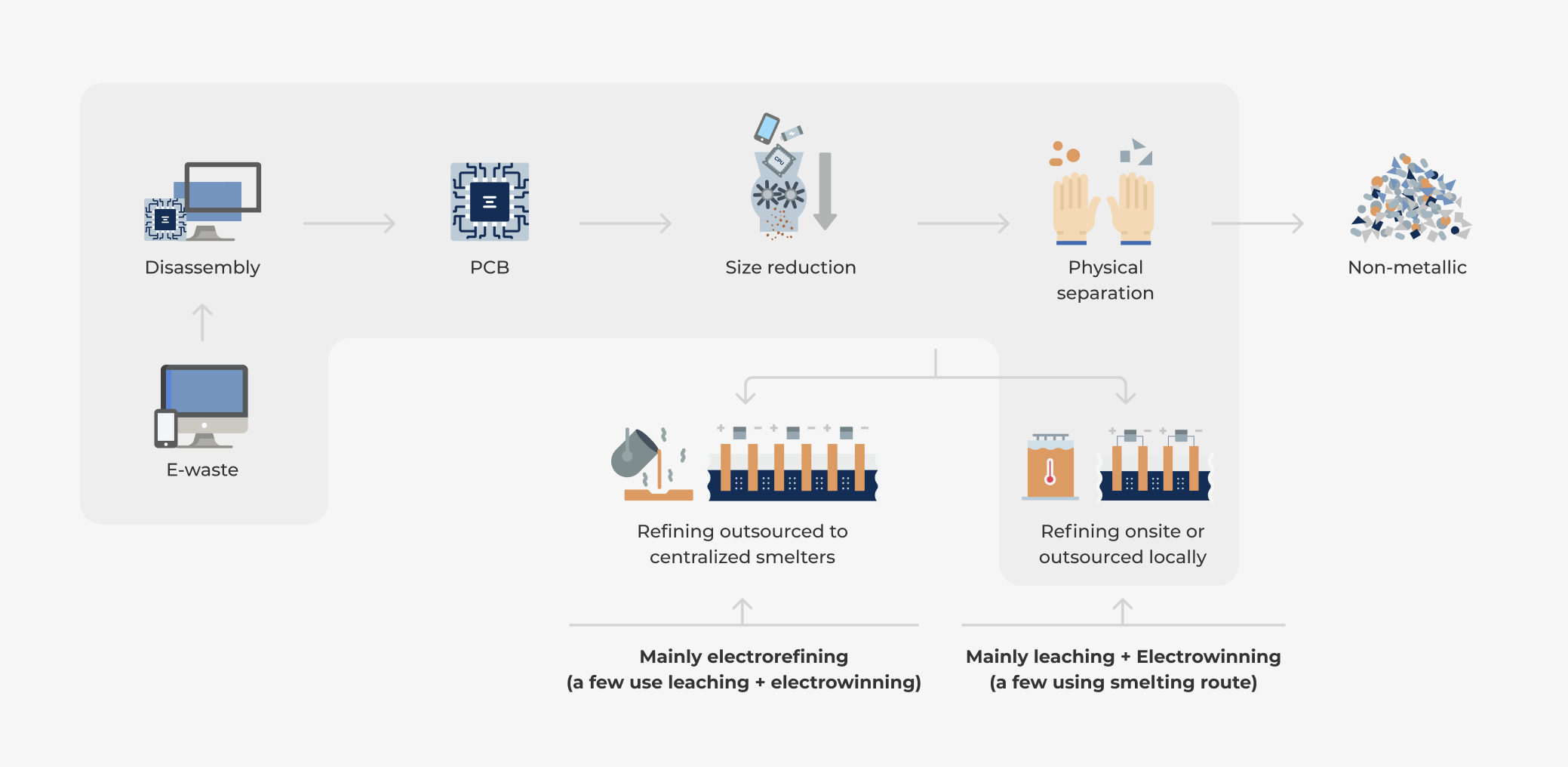
Story of one of the localized alternatives: Bioscope Technologies
Bioscope started in2019 with a vision to repatriate critical metals after the Brexit process and pandemic freight costs made PCB exports uneconomic. Backed by Innovate UK grants, the company moved from lab work to a pilot plant in Cambridge and is now scaling to commercial capacity.
Two different flow sheets underpin their approach:
Base case - acid leach and electrowinning
Sulfuric leach +emew electrowinning is suited for copper-rich streams, delivering a smaller footprint per tonne and similarly high current efficiency without acid mist.
Advanced method -bio-leach and electrowinning
Bio-leach + emew electrowinning – ideal for lower-grade feeds, with closed-loop oxidant regeneration and low energy usage.
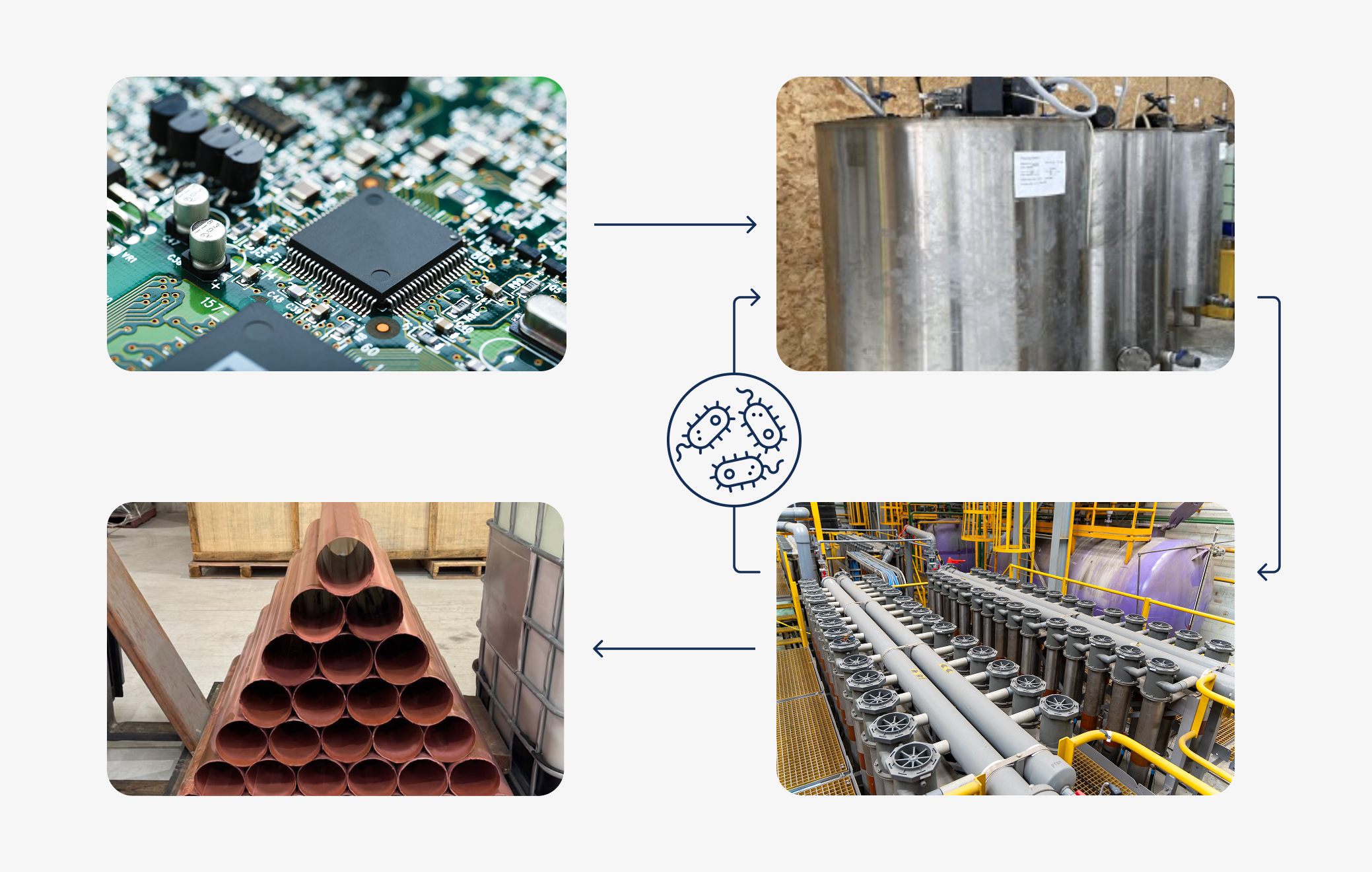
Currently, BioScope is building capacity and continuing the development of sustainable processes for multiple products while starting the full-scale commercial operation in a new site.
What This Means for the Value Chain
- Collectors & Pre-Processors can now choose between centralized, onsite, or regional refining based on Capex, logistics, and carbon goals.
- Smelters & Large Refiners are developing ways to enhance traceability, handle smaller lots, and explore service-based models.
- Policymakers see localized capacity as a path to resource security and job creation while tightening landfill bans.
Key Takeaways
- A mix of local refiners and smelters can deliver speed, traceability, and lower carbon miles.
- Copper can be recovered efficiently, and precious-metal recovery gets easier.
- Modular leach-and-electrowin technologies (like emew) make small-scale plants attainable, even on dilute or impure feeds.
- Collectors, refiners, OEMs, and regulators must collaborate to unlock the full value of e-waste.
Copper’s circular journey is no longer a concept. It’s unfolding in regional hubs worldwide. Understanding this shift will be crucial for anyone looking to provide sustainable and economic recycling options in the future.