What is SX-EW?
Hydrometallurgical extraction is an effective way to recover copper from low-grade copper ores.
But how is it done?
Heap leaching is the method most commonly chosen for copper recovery from oxide ores. An acidic solution is used to leach the metal, dissolving the copper into what is referred to as a pregnant leach solution (PLS). This solution is collected and purified by solvent extraction (SX). SX is a two-step process of loading the copper into an organic solution, followed by stripping the copper from the organic, into an aqueous solution.
The final step in the process is electrowinning the copper from the aqueous solution, producing pure copper cathode.
Impurities build within the electrolyte over time and can compromise the purity of the copper cathode if their concentrations are not decreased.
What can be done to prevent this?
A bleed of the electrowinning (EW) solution is required to combat this build-up of contaminants. Once this portion of solution is bled from the EW tankhouse it is often recycled within the SX-EW copper recovery circuit. Further problems arise when this bleed has high concentrations of copper, which is how emew technology can be used to make the SX-EW copper recovery process more efficient and more cost-effective. The benefit of adding on emew to an existing SX-EW system is its ability to extract any residual copper in the bleed and recover it as saleable copper cathode.
We are going to discuss the process of SX-EW for copper recovery, focusing specifically on the need for an EW bleed and how emew technologies can be an integral part of the copper recovery process to improve recoveries in the heap leach and increase production.
How is Cu recovered by SX-EW?
Copper recovery by SX-EW can be explained as a 4-step process. Figure 1 shows the flow of solutions and products within the SX-EW circuit.
The steps are as follows:
1) LEACH
- Low grade copper ore is leached, producing solid waste and copper PLS
2) EXTRACTION
- The copper PLS is sent for extraction where the copper is loaded into the organic phase, leaving a copper-barren leach liquor (raffinate) to be recycled back to the heap leach
3) STRIPPING
- The copper is stripped from the organic phase, into the aqueous phase, the organic is sent back to extraction
4) ELECTROWINNING
- The copper-loaded aqueous solution is electrowon, producing copper cathode as the final product, the spent electrolyte is recycled back for stripping
Plants bleed a portion of the EW electrolyte to control impurities and maintain cathode quality. Various impurities can cause detrimental effects when they build in the electrolyte.
Table 1 outlines these impurities and their affect on electrowinning and copper cathode quality.
.png)
Table 1. Impacts of Various Contaminants in EW Electrolyte
Constant recirculation of Fe2+, Fe3+, and/or Cl- causes their concentration to increase inside the EW tankhouse, leading to loss of current efficiency (CE) or poor quality of the deposit. A specific volume of this rich electrolyte is bled, and replaced by water.
So, how big is the bleed?
The electrolyte bleed ranges anywhere from 0-5%; majority of plants are in the 0-1% region. High concentration of iron is the most common reason for the bleed. Since this bleed still contains high concentrations of copper, >35 g/L, and acid >170 g/L, it is recycled within the SX-EW circuit to avoid any loss of copper.
Where is the bleed sent?
In the circuit, the bleed that has >30 g/L Cu is typically sent to the raffinate pond, PLS pond, SX-extraction stage, or the SX-wash stage, Figure 1. The disadvantages of recycling the bleed to these locations are as follows:
A) Raffinate Pond
- According to Fick’s Law, increasing the copper concentration in the raffinate decreases the leaching power of the raffinate, resulting in lower copper recovery from the heap
B) PLS Pond
- Typically, the acid concentration in the feed will need to be less than 5 g/L. Increased copper and acid concentrations in the SX stage reduces the recovery, this can be compensated by increasing the extractant concentration but will lead to increased carryover and loss of organic
C) Extraction Stage (E1)
- Higher acid to this stage will reduce the efficiency of the extraction
D) SX Wash Stage
- Increased acid concentration in the wash stage leads to more copper stripping & increase recycle load of copper to PLS which reduces capacity of extraction
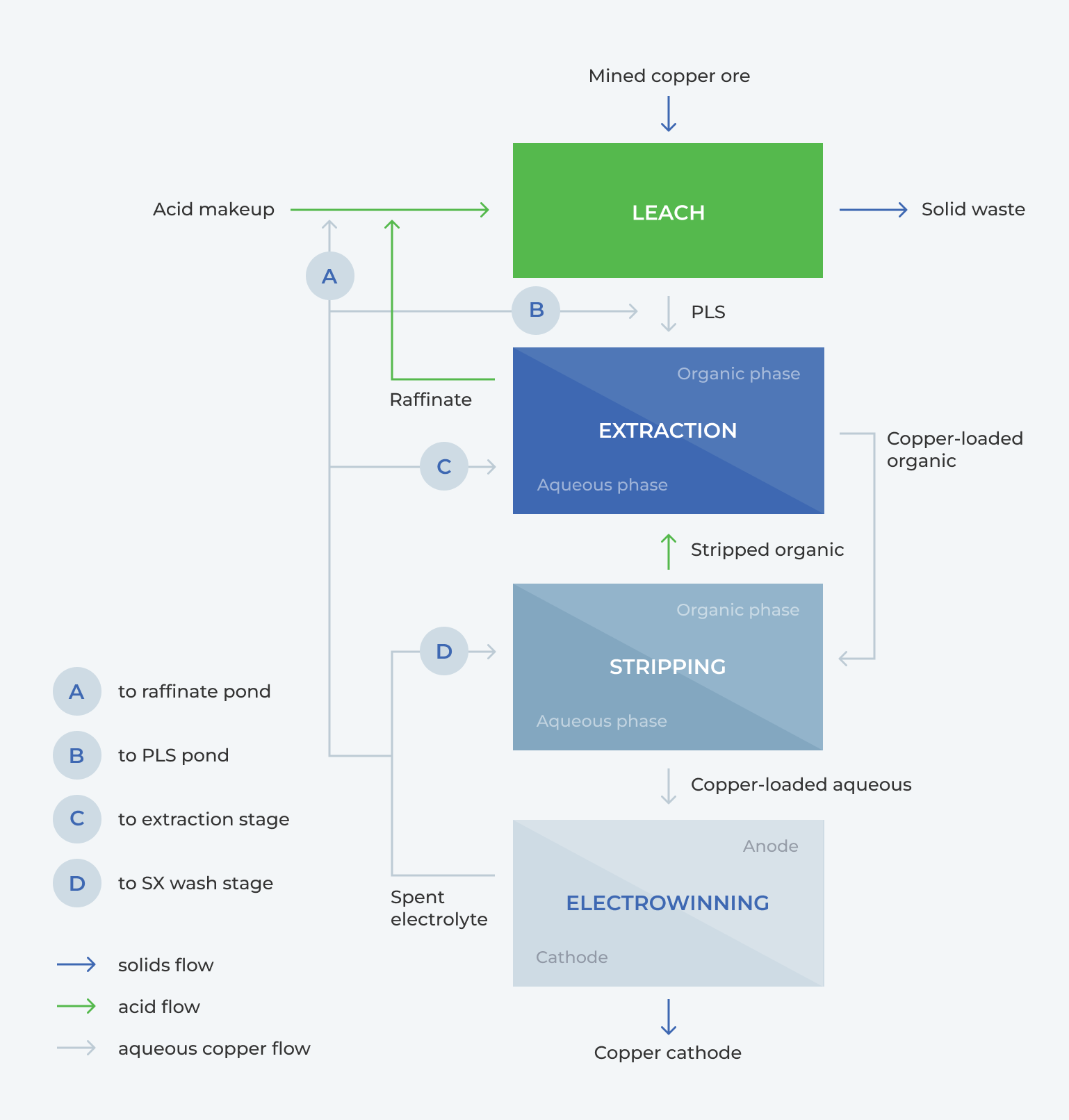
Fig. 1. Flow Diagram of Copper Recovery by SX-EW, showing possible routes for the spent electrolyte to be recycled within the circuit
An alternative to recycling the bleed is to electrowin the copper from the bleed; this low copper, high acid solution can then be sent to the raffinate (A) for higher leach recovery, or (if the acid concentration is not too high – 180-200 g/L) to stripping (D) for higher SX recovery. When the decopperized bleed solution after emew copper recovery is sent to the leach the leaching recoveries are improved.
How is this explained?
The main way to significantly increase the leaching capacity of the raffinate solution is by purifying the raffinate before sending it back to the heap, and this is where emew fits in.
How does emew help Cu Recovery with SX-EW?
The benefit of using emew in an SX-EW plant is for increased copper recovery – to decrease the recirculating copper load. A direct result of electrowinning the copper is a concurrent increase in acid which also helps improve the leaching efficiency. As discussed previously, there are serious implications to a high recirculating copper load.
emew can solve this problem.
Saleable copper cathode can be recovered from solutions as low as 1 g/L copper, and emew systems can deplete as low as 500 ppm. Even under extreme operating conditions, emew can produce high-quality, saleable copper cathode from highly contaminated solutions, with low concentrations of copper. One of the most important features of emew is that it can be added onto an existing SX-EW plant, Figure 2.
emew is modular.
A modular configuration means emew can easily be implemented to recovering additional copper units from the electrolyte bleed, preventing loss of copper, decreasing the copper recirculating load, increasing the acid returned to the heap, thereby increasing the overall effectiveness of the heap leach.
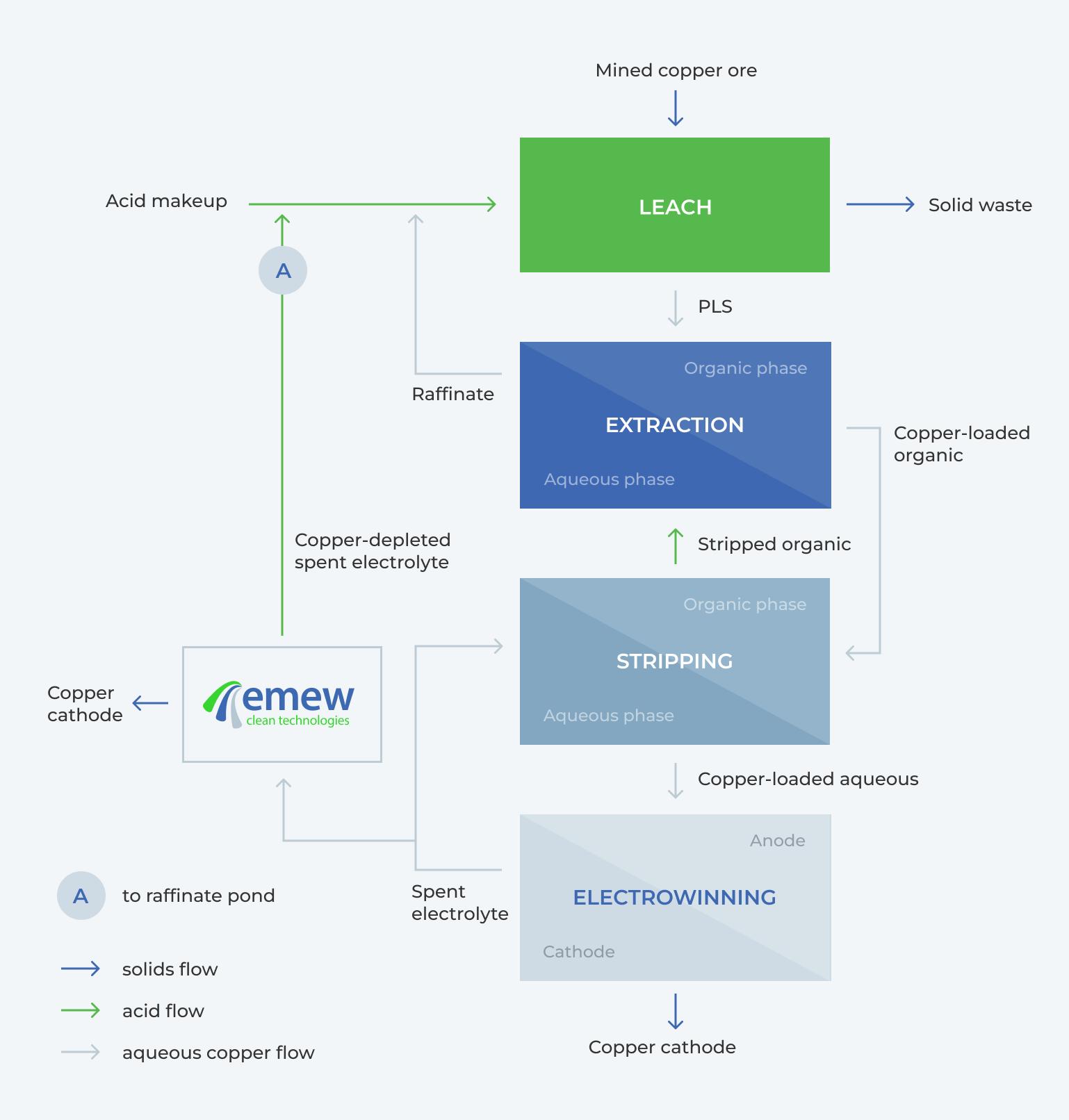
Fig. 2. Flow Diagram of Copper Recovery using SX-EW with emew
Is it possible to use conventional EW for this step?
Conventional EW cells can be used here, but they cannot operate as efficiently below 20 g/L, so it is not possible to deplete to as low of concentrations to realize the same benefits as with emew. Using emew for additional copper depletion adds value by increasing the amount of saleable copper produced, returning less copper / more acid to the heap, and reducing working capital.
Does emew equal increased value?
The CAPEX for emew is relatively low, especially when adding onto an existing plant, and when considering the payoff of the saleable copper produced, as well as the increased effectiveness of the leach when recycling acid that is free of copper. When the recycling copper load in a plant is high it represents high copper inventory and high working capital.
In other words, decreasing the copper load significantly increases the first pass copper recovery and overall profitability of a plant. The production capacity can be expanded when there is less copper recirculating; it also provides higher recovery of copper in the leach or in SX. Not only does copper depleted acid have a better effect on the leach recovery, it also can be used for filter washing – reducing copper losses from the circuit.
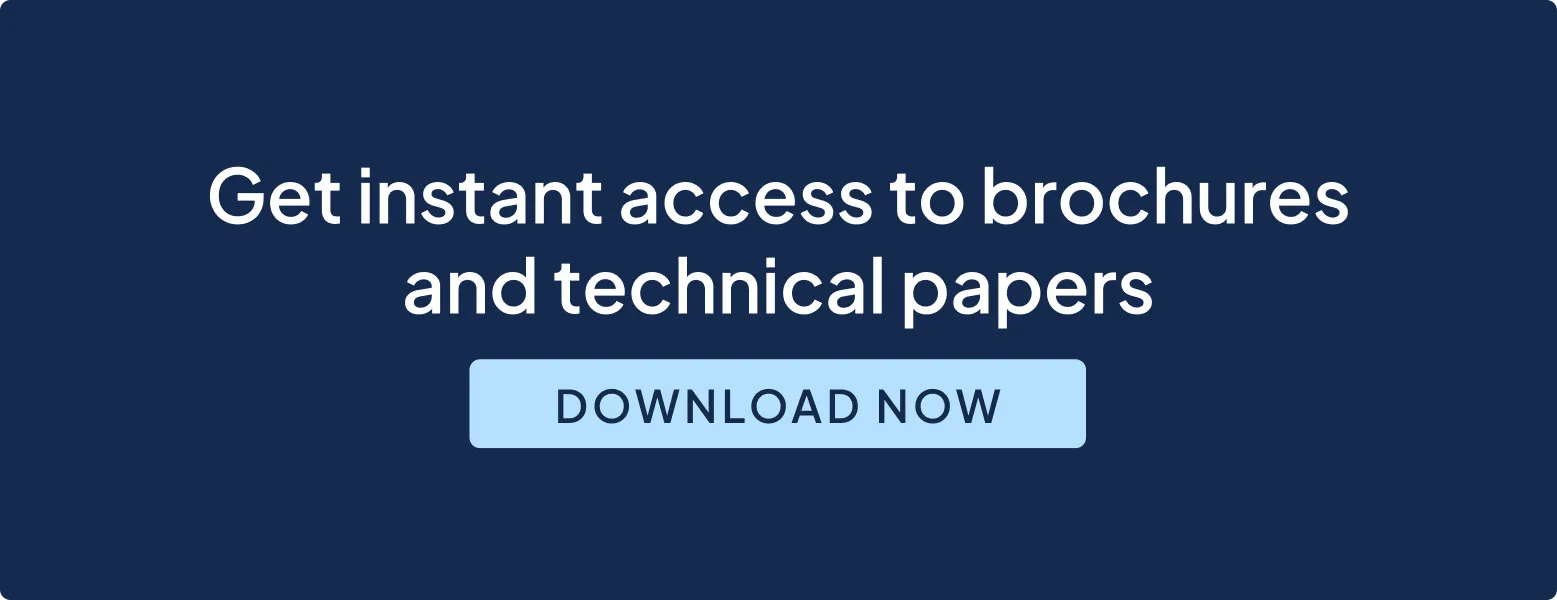
Tests lasting 29 days were run to compare the leach rate of recycling the spent electrolyte with and without emew treatment. When emew systems were used, there was an 8.9% increase in copper recovery of the leach (Badilla, 2013).
With the decrease in copper recirculation and increase in copper leaching, the plant can have its capacity expanded by 5-10% at a relatively low cost. An increase in production capacity is just one of the benefits of adding emew onto an existing SX-EW circuit; decreased acid requirements, lower recycled copper load, high process versatility, and a more effective circuit are some of the other advantages.
How does SX-EW-emew compare to SX-EW?
Comparing a SX-EW plant that incorporates emew to recover copper from the bleed to one that does not, the benefits and payback justify the capital to add emew into an existing circuit.
Decreasing the recirculating copper load allows for an increased recovery of copper in the leach and increased capacity of the SX-EW plant. Increasing recovery of copper by 5-10% will improve the profitability and decrease the working capital of the plant, with minimal capital outlay. By not removing the recirculating copper load, the overall copper recovery decreases and the overall operating expense is higher due to the fresh acid requirement to E1 and SX-Wash stages and lower recovery in the heap.
Adding emew into an existing SX-EW plant enables additional production to be realized without any additional mining as the incremental copper production comes from improved recovery of already mined and crushed ore. If this is done with direct solar power there is actually a possibility to produce zero carbon copper. The addition of emew in SX-EW circuits results in improved profitability and production.
References
Badilla, S., Haussmann, F., and Blumos, S. (2013). Recovery Improvements in Copper Heap Leaching by Using emew Technology. IIMCH, 4.
Dixon, R., et. al. (2007). Adding Value to LIX/SX/EW Operations by Recovering Copper from Bleed, Raffinate and Other Plant. Conference of Metallurgists.
Dresher, W. (2011). Innovations: How Hydrometallurgy and the SX/EW Process Made Copper the “Green” Metal. [online] Copper.org. Available at: https://www.copper.org/publications/newsletters/innovations/2001/08/hydrometallurgy.html[Accessed 2 Feb. 2018].
Lackie, J. (2013). The Dictionary of Cell & Molecular Biology (5th ed.). Academic Press.