When talking about electrowinning, copper, silver, and nickel always seem to be the center of attention. However, with the recent advancements in electric vehicles and electronics, it’s Cobalt’s time to shine.
This blog will cover the basics of cobalt electrowinning, giving you a full grasp on the topic in 3 minutes or less.
Cobalt is one of few metals that can be electrowon relatively easily, however, it does not come without its challenges. Cobalt has a more negative reduction potential than nickel, copper, silver and gold which means that solutions must be free of these impurities prior to electrowinning of cobalt.
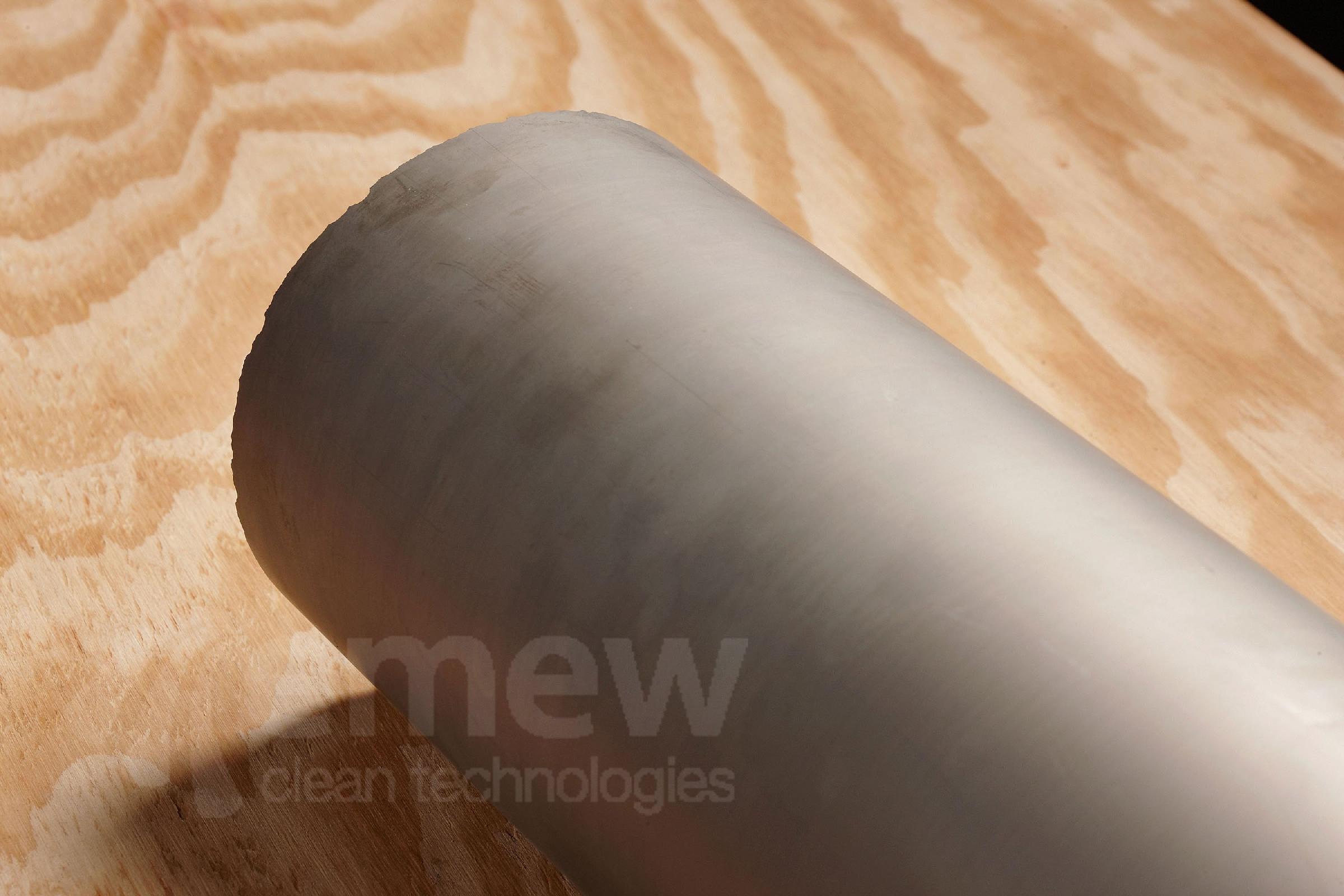
For a better understanding of reduction potentials and electrowinning, please refer to our video on the electrochemical series.
The point to be made is that Cobalt’s location on the series means it can be electrowon from almost any sulfate-based solution, with a couple caveats.
1) Proximity to Nickel
Cobalt has an electrochemical potential of E0 = -0.28 V, while Nickel’s is E0 = -0.25 V. If in solution together, it’s almost impossible to selectively electrowin either of these metals.
2) Impurities in Solution (Fe, Cr, Cu, Pb, Zn etc.)
Because cobalt has a negative electrochemical potential, it means that other metals are more likely to plate first if in the same solution.
These metals include: Au, Pt, Ag, Cu, Sn(II and IV), and Pb. These aren’t the only metals that can affect electrowinning of cobalt; manganese promotes sludge formation at the anode, while zinc causes internal stresses which causes cobalt to peel away from the cathode when electrowinning.
There are a few metals that generally cause difficulties during electrowinning and are not cobalt-specific, these are: Fe, Cr, As, Sb, Bi, Cl, F, and S.
3) Temperature and pH
Cobalt is a metal that can be a bit picky when it comes to conditions in which it will electrowin.
It doesn’t like being too hot, or too cold, and it definitely doesn’t like being at the wrong pH. Cobalt prefers a temperature range of 40-600C and a pH of below 2 or greater than 4.
These three parameters are not full-stops for electrowinning cobalt and are simple to overcome if you follow the right steps.
Nickel and cobalt are frequently found together in nature because of their similar physical and electrochemical properties; they are almost identical in atomic weight (Ni 58.69 u, Co 58.93 u) and both used in electrodes and alloys due to their traits of conductivity and corrosion resistance respectively.
Because nickel and cobalt are so often used together, it is possible to plate them together when electrowinning, preparing a nickel/cobalt alloy.
If wanting to electrowin pure cobalt in the presence of nickel or other metals and not create an alloy, there are other options:
A) Solvent Extraction (SX)
Cobalt and nickel can be selectively recovered by using SX to separate a solution into streams carrying cobalt and carrying nickel, providing electrowinning-ready electrolytes. SX will help remove other impurities as well, and the extractant can be selected based on the solution chemistry.
B) Precipitation
Precipitation is an effective method for impurity removal, either by precipitating the impurities or by precipitating the cobalt, which can then be re-dissolved in preparation for electrowinning.
C) Additives and Cell Design
There are certain additives that can be used in solution to help counteract the effects of certain impurities during electrowinning. Some impurities arise from the materials used in conventional electrowinning cells; for example, conventional cells often use lead alloy anodes and it is possible for the lead to corrode into the electrolyte, depending on the solution characteristics. Some advanced electrowinning cells, like emew, use specially designed titanium anodes with mixed-metal oxide coatings that are resistant to anode corrosion in most electrolytes.
The preference of cobalt to be in a hot, pH buffered solution, is due to the production of acid that occurs at the anode during electrowinning. This is very simply explained by the electrochemical reactions occurring within the cell.
Cathodic
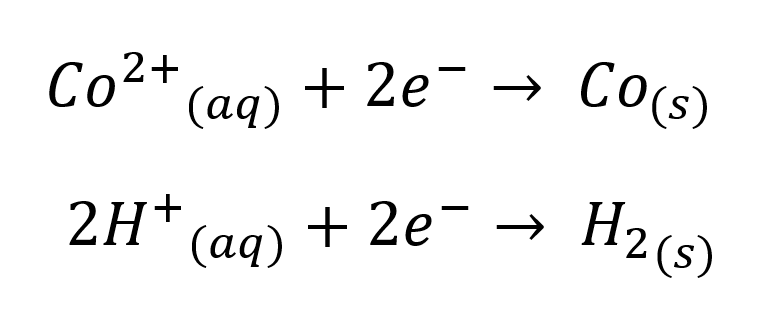
E0 = - 0.28 V
E0 = 0.00 V
Anodic
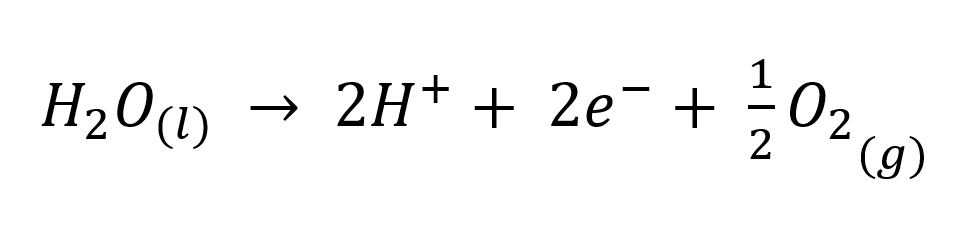
E0 = + 1.23 V
If the pH is not controlled, the acid generated will re-dissolve the plated cobalt and make the current efficiency appear lower than it truly is and inflate power costs, etc. Control of pH can also help avoid co-plating of impurities.
Temperature is another parameter that should be monitored; since the electrochemical reaction of cobalt to cobalt metal has a negative reduction potential, increasing temperature helps improve the rate of reaction as well as the current efficiency.
Now that you understand how to effectively electrowin cobalt from solution, here are some examples of streams that are well suited for cobalt-recovery and industries that require cobalt or nickel/cobalt cathode:
- Batteries (LCO, NMC, NCA, NiMH, etc.)
- Superalloys
- Hardmetals
- Ceramics/pigments
- Catalysts
- Magnets
- EV Manufacture
- Mines
- Scrap Recyclers
Cobalt takes a caring touch to electrowin, but with the right experience and understanding, it is possible to plate out pure, saleable cobalt cathode (or cobalt-nickel alloy) from a wide variety of sulphate-based solutions.
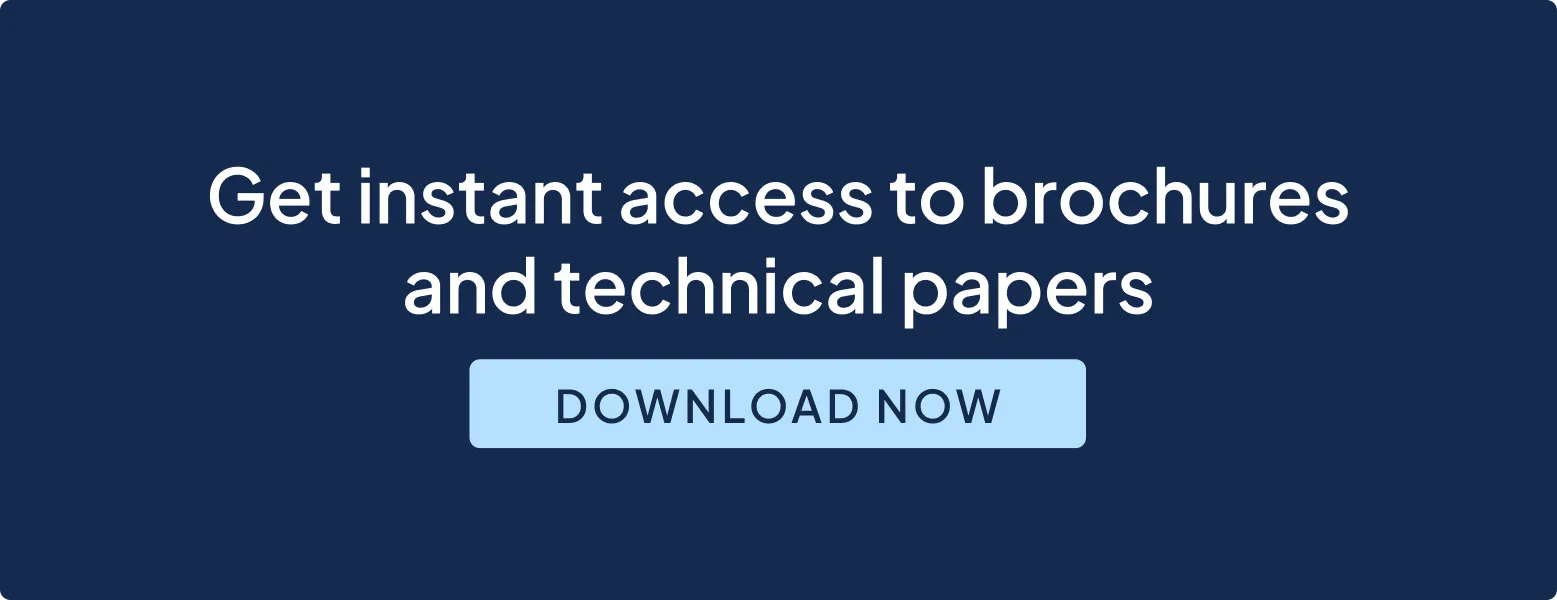
References
https://www.globalenergymetals.com/cobalt/cobalt-demand/
https://www.thoughtco.com/metal-profile-cobalt-2340131
https://emew.com/copper-refinery-bleed/
http://batteryuniversity.com/learn/article/types_of_lithium_ion
Wildenboer, R.A., 2018, ‘Mechanical Characterisation of Cobalt Electrowinning from Dilute Sulphate Solutions’, in Copper Cobalt Africa, incorporating the 9th Southern African Base Metals Conference, Southern African Institute of Mining and Metallurgy, Livingstone, Zambia, pp. 431-442.